Defektų kaina skirtinguose gamybos etapuose medienos pramonėje
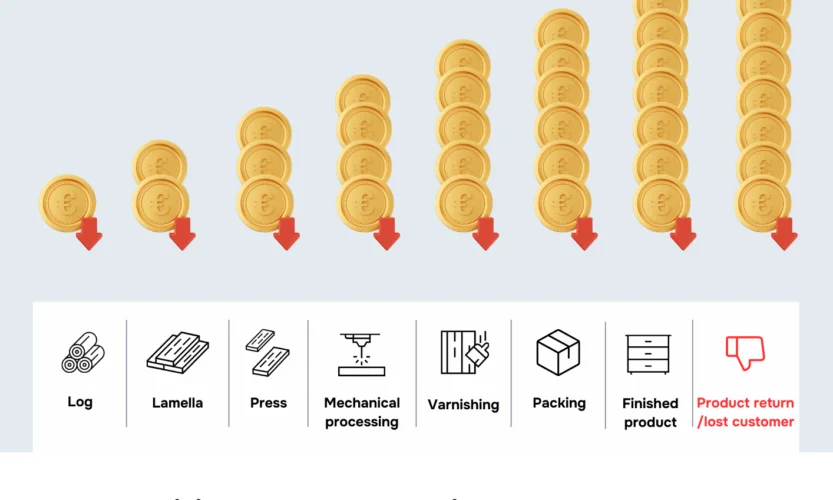
Defekto aptikimas vėlesniame baldų gamybos etape sukelia didesnes išlaidas, susijusias su papildomais remonto darbais, medžiagų nuostoliais, didesnėmis darbo sąnaudomis ir gamybos grafiko vėlavimais. Todėl defektų aptikimas kuo ankstesniuose procesuose yra esminis norint sumažinti išlaidas ir užtikrinti aukštą produktų kokybę. Su kokiais iššūkiais jūsų gamybos skyrius gali susidurti kiekviename etape? Ko reikėtų vengti?
Kokie produktų defektai gali pasitaikyti skirtinguose medienos apdorojimo procesuose?
Paimant baldų gamybos procesą kaip pavyzdį, defektai, kurie gali pasitaikyti bet kuriame medienos apdorojimo etape, yra šie:
Rąstai – rąstų etape gali pasitaikyti struktūriniai medienos defektai, tokie kaip mazgai, mazgėtumas, kreivumas ar įtrūkimai. Tai natūralūs medienos bruožai, kurie gali paveikti galutinio produkto kokybę.
Lamelės – lamelės gali turėti defektų, tokių kaip sluoksniavimosi ar įtrūkimai, kurie, pavyzdžiui, gali sumažinti medienos komponentų stiprumą ir stabilumą.
Presai – netinkamas lamelių klijavimas gali sukelti nekokybiškus sujungimus, kurie gali padidinti įtrūkimų ar sluoksnių atplėšimo riziką tolesniuose gamybos etapuose.
Apdorojimas – apdorojimo metu gali atsirasti defektų, tokių kaip nelygūs kraštai, paviršiaus netolygumai arba įtrūkimai, atsirandantys dėl netinkamo frezavimo ar pjovimo.
Lakavimas – netolygiai užteptas lakas gali sukelti negražų galutinio produkto išvaizdą ir sumažinti jo ilgaamžiškumą. Taip pat gali atsirasti oro burbuliukų ar dryžių.
Pakavimas – pakuojant medinius produktus gali pasitaikyti mechaninių pažeidimų, tokių kaip įbrėžimai, įtrūkimai ar skaldos, kurie gali sumažinti produkto estetinę ir funkcinę vertę. Dažniau vis dėlto pasitaiko ženklinimo klaidų: neteisingas EAN numeris, partijos numeris, etikečių kalba, kas gali sukelti visos partijos ar net viso konteinerio produkto grąžinimą.
Kiekvienas defektas vėlesniame procese padidina gamybos kaštus.
Brangiausi defektai gali pasireikšti galutiniame produkte. Pristatymo į klientą etape jau buvo patirti visi gamybos ir transportavimo kaštai. Tačiau tai nėra pagrindinė priežastis, kodėl gamintojo rizika šiuo atveju yra didžiausia. Defekto turinčio produkto pristatymas, ypač jei klientas ilgai laukė arba reikalavo, kad jis būtų surinktas, kaip baldų atveju, gali lemti klientų atsisakymą nuo įmonės. Naujo kliento įgijimo kaina yra daug didesnė nei esamo kliento išlaikymo, todėl šie kaštai yra ypač aktualūs gamintojui.
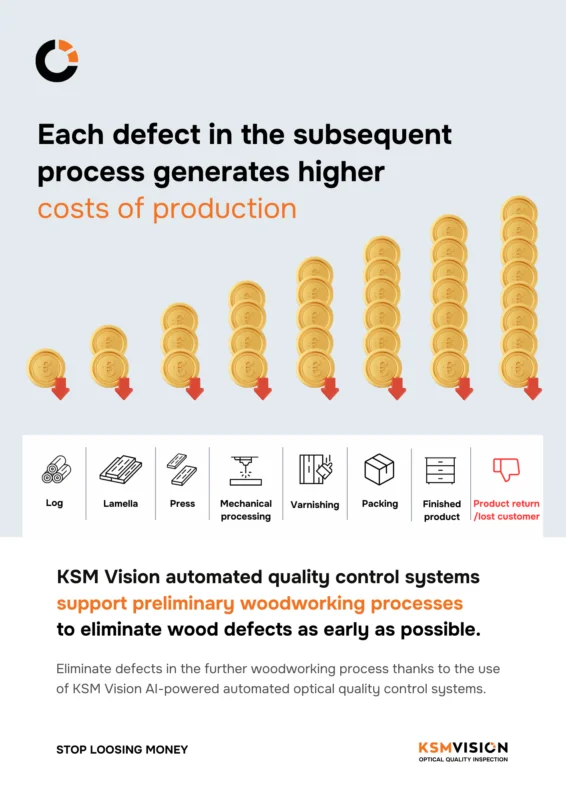
Gamybos kaštai didėja dėl defektų
Taigi, kaštai, susiję su defekto aptikimu vėlesniuose baldų gamybos etapuose, yra didesni dėl kelių priežasčių:
- Didėjantys medžiagų nuostoliai: Defekto atsiradimas vėlesniuose gamybos etapuose didina tikimybę, kad visą komponentą ar produktą teks atmesti arba atlikti didelius pakeitimus. Tai savo ruožtu lemia didesnius medžiagų nuostolius, nes medžiaga jau buvo apdorota pažangesniame gamybos etape.
- Didesnės remonto darbo sąnaudos: Vėlesniuose gamybos etapuose baldai gali būti jau praeitę per kelis procesus, tokius kaip pjovimas, apdorojimas, surinkimas, dažymas ir kt. Aptikus defektą šiuose etapuose, reikia atlikti pakartotinius darbus arba net visą gamybos procesą, kas reikalauja papildomų darbo ir medžiagų sąnaudų. Tai gali sukelti papildomas išlaidas darbo laikui ir viršvalandžiams.
- Gamybos grafiko vėlavimai: Defekto aptikimas vėlesniuose etapuose gali sukelti gamybos grafiko vėlavimus, nes reikės atlikti papildomas korekcines ar modifikavimo priemones. Šie vėlavimai gali sukelti papildomas išlaidas, susijusias su įrenginių prastovomis, praleistais pristatymo terminais ar būtinybe prailginti darbuotojų darbo valandas.
- Viso produkto atmetimas: Kai kuriais atvejais, kai defektas yra per rimtas arba nebeįmanoma jo ištaisyti, gali prireikti visiškai atmesti galutinį produktą. Nuostoliai, susiję su prarastomis medžiagomis ir darbu, dažnai būna žymiai didesni nei defekto aptikimo ir ištaisymo kaštai ankstesniuose etapuose.
- Įmonės įvaizdis: Jei defektai nėra aptinkami iki galutinio produkto etapo, tai gali neigiamai paveikti įmonės reputaciją. Klientai gali atsisakyti pirkti produktus iš įmonės, turinčios didelį defektų procentą.
Automatizuotos kokybės kontrolės sistemos kaip kaštų mažinimo šaltinis
Defektų aptikimas ankstyvuoju gamybos etapu yra svarbus dėl kelių priežasčių:
- Kaštai: Kuo ilgiau defektas lieka nepastebėtas, tuo brangiau gali kainuoti jo taisymas arba viso produkto atmetimas. Ankstyvas defekto aptikimas leidžia greitai reaguoti ir sumažinti finansinius nuostolius.
- Produkto kokybė: Medžio defektai gali ženkliai sumažinti galutinio produkto kokybę, tiek išvaizdos, tiek patvarumo prasme. Aptikus juos ankstyvame etape užtikrinama, kad galutinis produktas atitiks klientų lūkesčius tiek estetikos, tiek funkcionalumo požiūriu.
- Saugumas: Tam tikri defektai gali paveikti produkto naudojimo saugumą, ypač kalbant apie baldus ar medines konstrukcijas. Ankstyvas potencialių pavojų aptikimas leidžia greitai juos pašalinti prieš produktui pasiekiant galutinį vartojimą.
- Gamybos proceso efektyvumas: Defektų aptikimas ankstyvame etape leidžia greitai įsikišti, taip sumažinant gamybos vėlavimus. Taip pat užkertama kelias reikalingumui pakartoti gamybos procesus vėlesniuose etapuose, kas gali ženkliai sumažinti produktyvumą ir padidinti kaštus.
- Įmonės reputacija: Kokybiški produktai yra svarbi teigiamo įmonės įvaizdžio kūrimo dalis. Defektų aptikimas ankstyvame etape ir klientams tiekiami produktai, atitinkantys jų lūkesčius, padeda išlaikyti reputaciją kaip tvirtų ir patikimų produktų gamintoją.
Kuo ankstesniame etape aptinkamas defektas, tuo mažesni gamintojo kaštai ir problemos.
Kokybės kontrolės efektyvumą aptikti defektus kuo anksčiau gamybos procese galima padidinti naudojant aukštos kokybės automatizuotas vaizdo sistemas kokybės kontrolei. Su automatizuotomis sistemomis patikros efektyvumas yra žymiai didesnis nei su rankine patikra, atliekama operatorių. Sistemos „nepavargsta” ir „neišeina atostogų.” Investicijų grąža į kokybės tikrinimo sistemas yra palyginti trumpa, dėl sumažėjusių darbo sąnaudų, susijusių su rankine patikra.
Automatizuota kokybės kontrolė medienos apdorojimo pramonėje
Automatizuotų kokybės kontrolės sistemų naudojimas medienos apdorojimo pramonėje suteikia daugybę svarbių privalumų:
- Tokios sistemos yra itin tikslios ir patikimos. Dėka tikslių algoritmų ir tikslinių jutiklių jos gali aptikti net mažiausius defektus medžiagoje su dideliu tikslumu, pašalindamos defektų praleidimo riziką.
- Automatizuotos kokybės kontrolės sistemos veikia greitai ir efektyviai. Jos geba apdoroti didelius medžiagos kiekius per trumpą laiką, leidžiančios greitai identifikuoti defektus ankstyvose gamybos stadijose. Tai, savo ruožtu, leidžia greitai įsikišti ir atlikti remontą, mažinant nuostolius, susijusius su brokuotais produktais.
- Naudojant automatizuotas kokybės kontrolės sistemas, sutaupoma laiko ir kaštų. Tai pašalina poreikį atlikti rankines patikras, taupydama darbuotojų laiką ir mažindama gamybos kaštus. Be to, greitas defektų aptikimas ankstyvosiose gamybos stadijose sumažina riziką, kad teks atmesti visus produktų partijus, taip generuojant papildomas taupymo galimybes.
- Tai leidžia tiksliai dokumentuoti visus atliktus matavimus ir vertinimus. Ši dokumentacija gali būti naudinga tiek vidiniams tikslams, tiek santykiuose su klientais, leidžiant sekti medienos kokybę įvairiuose gamybos etapuose ir palengvinant galimų skundų sprendimą.
- Teikia duomenis apie defektų dažnumą ir jų vietą. Ši informacija gali būti naudojama siekiant nustatyti problemas gamybos procesuose ir atlikti atitinkamas tobulinimo priemones, vedančias į tolesnį medienos produktų gamybos efektyvumo ir kokybės gerinimą. Viso to pasekoje, automatizuotos kokybės kontrolės sistemos yra pagrindinis įrankis, užtikrinant aukštą kokybę ir medienos apdorojimo proceso efektyvumą.
KSM Vision automatizuotos optinės kokybės kontrolės sistemos palaiko pradinius medienos apdorojimo procesus, kad defektai būtų pašalinti kuo anksčiau. Naudodamos KSM Vision automatizuotas optines kokybės kontrolės sistemas, pagrįstas dirbtiniu intelektu (deep learning AI), galima pašalinti rankinę patikrą iš proceso ir taip padidinti patikros efektyvumą. KSM Vision sistemose naudojamos neuroninės tinklai yra apmokyti konkrečioms, sunkiai sprendžiamoms problemoms. Optinės kokybės kontrolės sistemos gali, pavyzdžiui, atskirti įtrūkimą nuo pjūvio žymės arba dervos kišenę nuo per didelio apšvietimo. Defektų klasifikavimas šiose sistemose yra žymiai efektyvesnis nei rankinė patikra.