The cost of defects at different stages of production in the timber industry
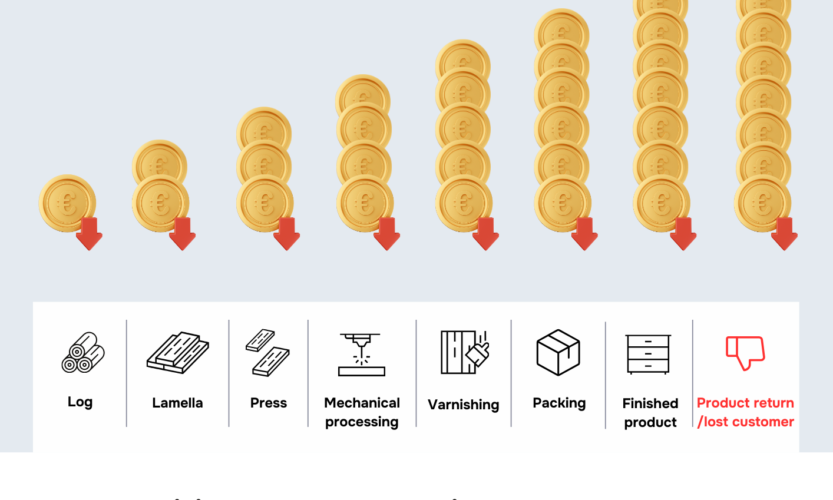
Detection of a defect at a later stage in the production of a piece of furniture generates higher costs associated with additional repair work, material losses, higher labor costs and delays in the production schedule. Therefore, detecting defects as early as possible in the process is key to minimizing costs and ensuring high product quality. What can your production department encounter at each stage? What should you avoid?
What product defects can occur at different stages of woodworking process?
Taking the furniture manufacturing process as an example, among the defects that can occur at any stage of the wood processing process are:
- Log – at the log stage, structural defects in the wood can occur, such as knots, knottyness, curvature or cracks. These are natural characteristics of the wood that can affect the quality of the final product.
- Lamellas – lamellas can have defects in the form of delamination or cracks, which can, for example, lead to a reduction in the strength and stability of wood components.
- Presses – improper gluing of lamellas can lead to poor quality joints, which can increase the risk of cracking or peeling of layers in further stages of production.
- Machining: defects in the form of uneven edges, surface irregularities or cracks due to improper milling or cutting may occur during wood machining.
- Varnishing: unevenly applied varnish can lead to an unsightly appearance of the final product and reduce its durability. Air bubbles or streaks may also appear.
- Packaging: during the packaging of wooden products, mechanical damage such as scratches, cracks or chips can occur, which can reduce the aesthetic and functional value of the product. More often, however, there can be labeling errors: wrong EAN # batch number, label language, which can jump the return of an entire batch or even a container of product.
Each defect in the subsequent process increases production costs.
The most costly of defects can occur for the finished product. At the stage of delivering the product to the customer, all manufacturing and transportation costs have been incurred. However, this is not what makes the manufacturer’s risk in this case the greatest. Delivery of a defective product, especially if the customer has waited a long time for it or required it to be assembled as in the case of furniture, can result in the customer abandoning the company. The cost of acquiring a new customer is much higher than retaining an existing one, so this cost is especially acute for the manufacturer.
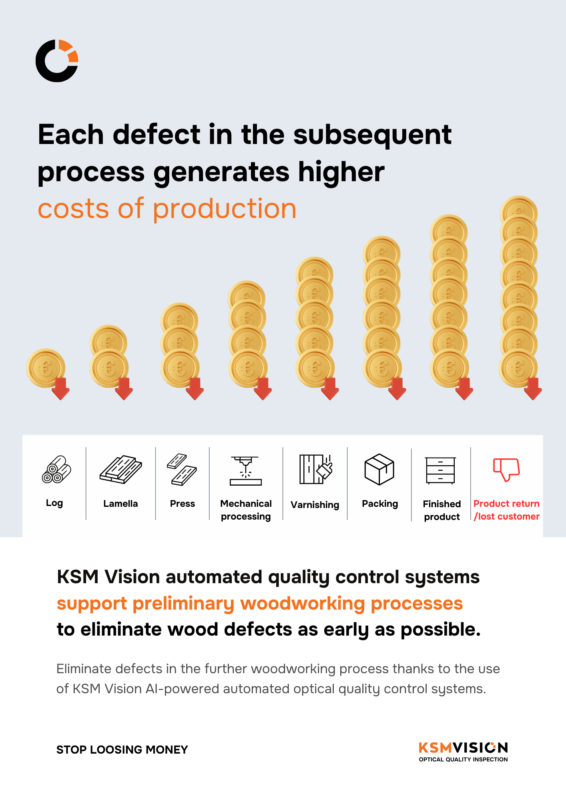
Production costs increase due to defects
Thus, the costs associated with detecting a defect at a later stage of furniture production are higher for several reasons:
- Increased material losses: In the event of a defect at a later stage of production, there is a greater risk that the entire component or product will have to be rejected or undergo major modifications. This, in turn, leads to higher material losses because the material has already been processed to a more advanced stage of production.
- Higher repair labor costs: At later stages of production, a piece of furniture may already have undergone multiple processes, which may include cutting, machining, assembly, painting, etc. When a defect is discovered at these stages, it is necessary to redo parts or even the entire production process, which requires additional labor and materials. This can incur additional costs in terms of labor time and overtime.
- Delays in the production schedule: Detection of a defect at a later stage can cause delays in the production schedule, as additional corrective or modification actions will need to be taken. These delays can lead to additional costs associated with machine downtime, missed delivery dates or the need for extended employee hours.
- Rejecting the entire product: In some cases, when the defect is too severe or beyond repair, it may be necessary to reject the finished product altogether. The costs associated with lost material and labor are usually much higher than the cost of detecting and correcting the defect at an earlier stage.
- Company image: If defects are not detected until the finished product stage, the company’s reputation can be negatively affected. Customers may be discouraged from buying products from a company that has a history of high defect rates.
Automated quality control systems as a source of cost reduction
Capturing defects early in the production process is important for several reasons:
- Cost: The longer a defect goes undetected, the more costly it can be to repair it or reject the entire product. Catching a defect early allows a quick response and minimizes financial losses.
- Product quality: Defects in wood can significantly reduce the quality of the final product, both in terms of appearance and durability. Catching them at an early stage helps ensure that the final product meets customer expectations in terms of aesthetics and functionality.
- Safety: Certain defects can affect the safety of a product’s use, especially when it comes to furniture or wooden structures. Early detection of potential hazards allows them to be quickly eliminated before the product reaches final use.
- Manufacturing process efficiency: Catching defects at an early stage enables quick intervention, which in turn minimizes production delays. It also prevents the need to repeat production processes at later stages, which can significantly reduce productivity and increase costs.
- Company reputation: Quality products are an important part of building a positive corporate image. Catching defects at an early stage and providing customers with products that meet their expectations helps maintain a reputation as a manufacturer of solid and reliable products.
The earlier a defect is detected, the lower the manufacturer’s costs and problems.
The effectiveness of quality control to detect defects at the earliest possible stage of the production process can be increased by high-quality automated vision systems for quality control. With automated systems, inspection efficiency is much higher than with manual inspection by operators. Systems “don’t get tired” and “don’t go on layoffs.” The return on investment for quality inspection systems is relatively short, due to the reduction in job costs associated with manual inspection.
Automated quality control in the woodworking industry
The use of automated quality control systems in wood processing brings a number of important benefits:
- Such systems are highly precise and reliable. Thanks to precise algorithms and accurate sensors, they are able to detect even the smallest defects in the wood material with high accuracy, eliminating the risk of overlooking defects.
- Automated quality control systems operate quickly and efficiently. They are capable of processing large volumes of material in a short period of time, allowing defects to be quickly identified at early stages of production. This, in turn, enables rapid intervention and repair, minimizing losses associated with defective products.
- Using automated quality control systems contributes to time and cost savings. It eliminates the need for manual inspections, saving workers’ time and reducing production costs. In addition, rapid identification of defects at earlier stages of production minimizes the risk of having to reject entire batches of products, leading to additional savings.
- Enable accurate documentation of all measurements and evaluations carried out. This documentation can be useful for internal purposes, as well as in customer relations, allowing wood quality to be tracked at various stages of production and facilitating the resolution of potential complaints.
- Provide data on the frequency of defects and their location. This information can be used to identify problems in production processes and make appropriate improvements, leading to further improvements in the efficiency and quality of wood product production. All in all, automated quality control systems are a key tool in ensuring the high quality and efficiency of the wood processing process.
KSM Vision’s automated optical quality control systems support initial woodworking processes to eliminate defects from the process as early as possible. By using KSM Vision’s automated optical quality control systems based on artificial intelligence (deep learning AI), it is possible to eliminate manual inspection from the process and thus increase inspection efficiency. The neural networks used in KSM Vision systems are trained for specific, hard-to-solve problems. Optical quality control systems can, for example, distinguish between a crack and a saw mark, or a resin pocket and overexposure. Defect classification here is much more efficient than manual inspection.