Koszty defektów na różnych etapach produkcji w przemyśle drzewnym
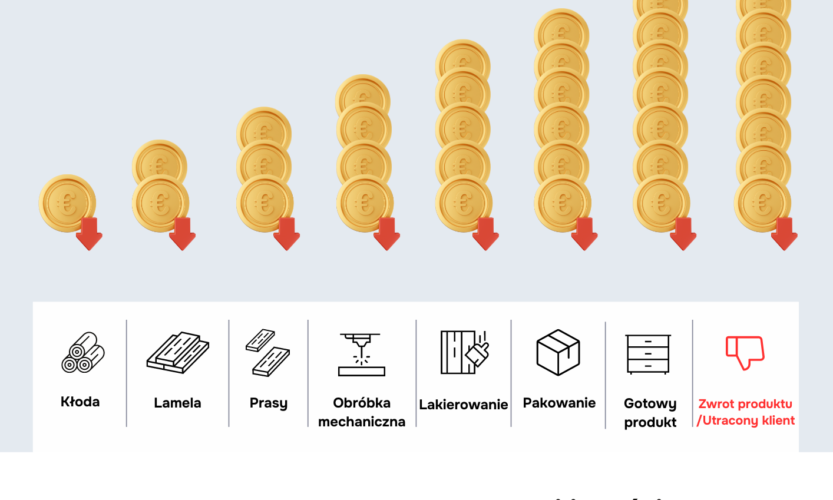
Wykrycie defektu na późniejszym etapie produkcji mebla generuje większe koszty związane z dodatkowymi pracami naprawczymi, stratami materiałowymi, wyższymi kosztami pracy i opóźnieniami w harmonogramie produkcji. Dlatego wykrycie defektów jak najwcześniej w procesie jest kluczowe dla minimalizacji kosztów i zapewnienia wysokiej jakości produktów. Co może spotkać Twój dział produkcji na każdym z etapów? Czego unikać?
Jakie wady produktów mogą wystąpić na różnych etapach obróki drewna?
Przyjmując do analizy dla przykładu proces produkcji mebla, wśród defektów, jakie mogą wystąpić na każdym etapie procesu przetwórstwa drewna, są między innymi:
- Kłoda – na etapie kłody mogą wystąpić wady strukturalne drewna, takie jak sęki, sękowatość, krzywizna czy pęknięcia. Są to naturalne cechy drewna, które mogą mieć wpływ na jakość finalnego produktu.
- Lamela – lamela może mieć wady w postaci rozwarstwienia lub pęknięć, które mogą przykładowo prowadzić do obniżenia wytrzymałości i stabilności elementów drewnianych.
- Prasy – niewłaściwe klejenie lamel może prowadzić do słabej jakości połączeń, co może zwiększyć ryzyko pęknięć lub odspajania się warstw w dalszych etapach produkcji.
- Obróbka mechaniczna: podczas obróbki mechanicznej drewna mogą występować defekty w postaci nierównych krawędzi, nierówności powierzchni lub pęknięć spowodowanych nieprawidłowym frezowaniem lub cięciem.
- Lakierowanie: nierównomiernie nałożony lakier może prowadzić do nieestetycznego wyglądu produktu końcowego oraz obniżenia jego trwałości. Mogą pojawić się także bąble powietrza lub zacieki.
- Pakowanie: podczas pakowania drewnianych produktów mogą wystąpić uszkodzenia mechaniczne, takie jak zarysowania, pęknięcia lub odpryski, które mogą obniżyć wartość estetyczną i funkcjonalną produktu. Częściej jednak mogą mieć miejsce błędy na etykietach: błędny EAN # numer serii, język etykiety, które potrafią skoczyć się zwrotem całej serii, a nawet kontenera produktu.
Każdy defekt w kolejnym procesie zwiększa koszty produkcji.
Najbardziej kosztowne z wad mogą wystąpić dla gotowego produktu. Na etapie dostarczenia produktu do klienta poniesione zostały wszystkie koszty wytworzenia i transportu. Jednak to nie to sprawia, że ryzyko producenta w tym przypadku jest największe. Dostarczenie wadliwego produktu, szczególnie jeśli klient czekał na niego długo lub wymagał od niego montażu jak w przypadku mebli, może skonczyć się rezygnacją klienta z usług firmy. Koszt pozyskania nowego klienta jest dużo wyższy niż utrzymania istniejącego, dlatego ten koszt jest wyjątkowy dotkliwy dla producenta.
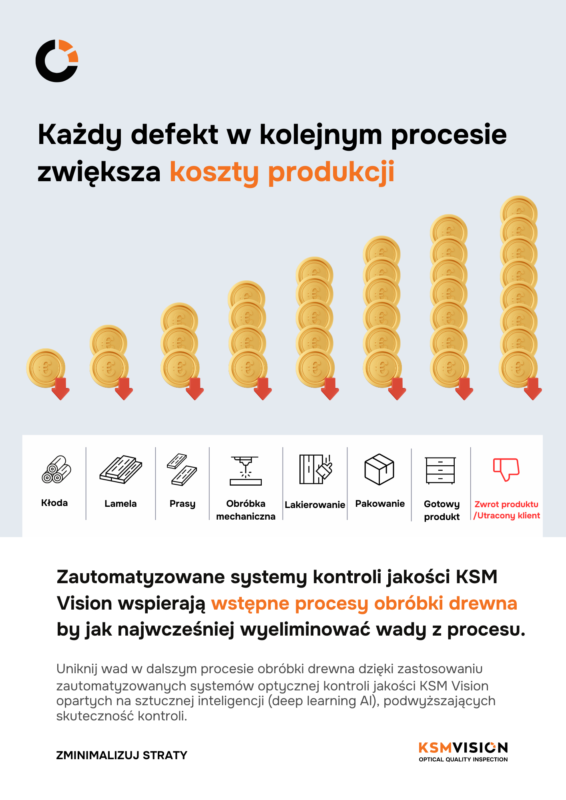
Wzrost kosztów produkcji spowodowany wadami
Tym samym koszty związane z wykryciem defektu na późniejszym etapie produkcji mebla są większe z kilku powodów:
- Zwiększone straty materiałowe: W przypadku defektu na późniejszym etapie produkcji istnieje większe ryzyko, że cały element lub produkt będzie musiał zostać odrzucony lub poddany poważnym modyfikacjom. To z kolei prowadzi do większych strat materiałowych, ponieważ materiał został już przetworzony na bardziej zaawansowany etap produkcji.
- Wyższe koszty pracy naprawczej: Na późniejszych etapach produkcji, mebel może zostać już poddany wielu procesom, co może obejmować cięcie, obróbkę, montaż, lakierowanie itp. Gdy defekt zostanie wykryty na tych etapach, konieczne jest ponowne przeprowadzenie części lub nawet całego procesu produkcyjnego, co wymaga dodatkowego nakładu pracy i materiałów. To może wiązać się z dodatkowymi kosztami związanymi z czasem pracy i nadgodzinami.
- Opóźnienia w harmonogramie produkcji: Wykrycie defektu na późniejszym etapie może spowodować opóźnienia w harmonogramie produkcji, ponieważ konieczne będzie podjęcie dodatkowych działań naprawczych lub modyfikacyjnych. Opóźnienia te mogą prowadzić do dodatkowych kosztów związanych z przestoju maszyn, utratą terminów dostaw czy koniecznością wydłużenia czasu pracy pracowników.
- Odrzucenie całego produktu: W niektórych przypadkach, gdy defekt jest zbyt poważny lub nie do naprawienia, konieczne może być całkowite odrzucenie gotowego produktu. Koszty związane z utraconym materiałem i pracą są zazwyczaj znacznie wyższe niż koszty wykrycia i poprawy defektu na wcześniejszym etapie.
- Wizerunek firmy: Jeśli defekty są wykrywane dopiero na etapie gotowego produktu, może to negatywnie wpłynąć na reputację firmy. Klienci mogą zrażać się do zakupu produktów od firmy, która ma historię wysokiej liczby defektów.
Zautomatyzowane systemy kontroli jakości jako źródło ograniczenia kosztów
Wychwytywanie defektów na wczesnym etapie w procesie produkcji jest istotne z kilku powodów:
- Koszty: Im dłużej defekt pozostaje niewykryty, tym kosztowniejsza może być jego naprawa lub odrzucenie całego produktu. Wczesne wychwycenie defektu pozwala na szybką reakcję i minimalizację strat finansowych.
- Jakość produktu: Defekty w drewnie mogą znacznie obniżyć jakość końcowego produktu, zarówno pod względem wyglądu, jak i wytrzymałości. Wychwycenie ich na wczesnym etapie pozwala na zapewnienie, że finalny produkt będzie spełniał oczekiwania klientów pod względem estetyki i funkcjonalności.
- Bezpieczeństwo: Niektóre defekty mogą wpłynąć na bezpieczeństwo użytkowania produktu, zwłaszcza jeśli chodzi o meble czy konstrukcje drewniane. Wczesne wykrycie potencjalnych zagrożeń pozwala na ich szybką eliminację, zanim produkt trafi do użytku końcowego.
- Efektywność procesu produkcyjnego: Wychwycenie defektów na wczesnym etapie umożliwia szybką interwencję, co z kolei minimalizuje opóźnienia w produkcji. Zapobiega to także konieczności powtarzania procesów produkcyjnych na późniejszych etapach, co może znacząco obniżyć wydajność i zwiększyć koszty.
- Wizerunek firmy: Produkty wysokiej jakości są ważnym elementem budowania pozytywnego wizerunku firmy. Wychwycanie defektów na wczesnym etapie i dostarczanie klientom produktów, które spełniają ich oczekiwania, pomaga w utrzymaniu reputacji jako producenta solidnych i rzetelnych wyrobów.
Im wcześniej wykryty defekt, tym mniejsze koszty i problemy producenta.
Skuteczność kontroli jakości celem wykrycia wad na jak najwcześniejszym etapie podwyższają wysokiej jakości zautomatyzowane systemy wizyjne do kontroli jakości. W przypadku zautomatyzowanych systemów skuteczność kontroli jest dużo wyższa niż w przypadku inspekcji manualnej przez operatorów. Systemy „nie męczą się” i „nie chodzą na zwolnienia”. Zwrot z inwestycji w systemy kontroli jakości jest relatywnie krótki, z uwagi na ograniczenie kosztów stanowisk związanych z inspekcją manualną.
Zautomatyzowana kontrola jakości w przemyśle drzewnym
Wykorzystanie zautomatyzowanych systemów kontroli jakości w procesie przetwórstwa drewna przynosi szereg istotnych korzyści:
- Tego rodzaju systemy są wysoce precyzyjne i niezawodne. Dzięki precyzyjnym algorytmom i dokładnym czujnikom są one w stanie wykrywać nawet najmniejsze defekty w materiale drewnianym z dużą dokładnością, co eliminuje ryzyko przeoczenia wad.
- Zautomatyzowane systemy kontroli jakości działają szybko i efektywnie. Są one zdolne do przetwarzania dużych ilości materiału w krótkim czasie, co umożliwia szybką identyfikację defektów na wczesnych etapach produkcji. To z kolei umożliwia szybką interwencję i naprawę, minimalizując straty związane z wadliwymi wyrobami.
- Korzystanie z zautomatyzowanych systemów kontroli jakości przyczynia się do oszczędności czasu i kosztów. Eliminuje ono konieczność przeprowadzania ręcznych inspekcji, co pozwala zaoszczędzić czas pracowników oraz zmniejszyć koszty produkcji. Ponadto, szybka identyfikacja defektów na wcześniejszych etapach produkcji minimalizuje ryzyko konieczności odrzucenia całych partii wyrobów, co prowadzi do dodatkowych oszczędności.
- Umożliwiają dokładną dokumentację wszystkich przeprowadzonych pomiarów i ocen. Ta dokumentacja może być przydatna do celów wewnętrznych, jak i w relacjach z klientami, umożliwiając śledzenie jakości drewna na różnych etapach produkcji oraz ułatwiając rozwiązywanie ewentualnych reklamacji.
- Dostarczają danych na temat częstotliwości występowania defektów i ich lokalizacji. Te informacje mogą być wykorzystane do identyfikacji problemów w procesach produkcyjnych i wprowadzenia odpowiednich ulepszeń, co prowadzi do dalszej poprawy efektywności i jakości produkcji drewnianych wyrobów. W sumie, zautomatyzowane systemy kontroli jakości stanowią kluczowe narzędzie w zapewnianiu wysokiej jakości i efektywności procesu przetwórstwa drewna.
Zautomatyzowane systemy wizyjne kontroli jakości KSM Vision wspierają wstępne procesy obróbki drewna, by jak najwcześniej wyeliminować wady z procesu. Dzięki zastosowaniu zautomatyzowanych systemów optycznej kontroli jakości KSM Vision opartych na sztucznej inteligencji (deep learning AI), możliwe jest wyeliminowanie inspekcji manualnej z procesu i tym samym podwyższenie skuteczności kontroli. Sieci neuronowe stosowane w systemach KSM Vision są trenowane pod konkretne, trudne do rozwiązania problemy. Optyczne systemy kontroli jakości potrafią przykładowo rozróżnić pęknięcie od śladów po pile albo kieszeń żywiczną od przeżywiczenia. Klasyfikacja defektów jest tu dużo skuteczniejsza niż w przypadku inspekcji manualnej.