Wdrożenie systemu wizyjnej kontroli jakości w mleczarstwie
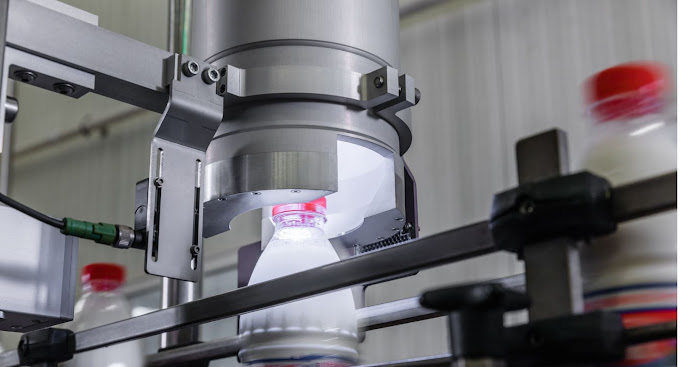
Droga od jednego do 6 systemów wizyjnej kontroli jakości zainstalowanych na 6 liniach produkcyjnych Grupy MLEKOVITA.
- Grupa Mlekovita
- Co obejmowała inspekcja linii produkcyjnych w mleczarstwie systemami KSM Vision?
- Wyzwania i zaproponowane rozwiązanie optymalizacji kontroli jakości
- Dlaczego Grupa Mlekovita wybrała systemy kontroli jakości KSM Vision oparte sieciach neuronowych?
- Co sprawia, że firmie produkującej produkty mleczarskie opłaca się i zwraca inwestycja w wizyjne systemy kontroli jakości?
Nie ma rozwoju bez przemyślanych inwestycji.
Dariusz Sapiński, Prezes Zarządu Grupy MLEKOVITA
Grupa Mlekovita
Grupa MLEKOVITA to największa grupa mleczarska w Europie Środkowo-Wschodnie o ponad 90-letniej tradycji. Firma eksportuje swoje produkty do 167 krajów na całym świecie.
Początkowo zlecenie KSM Vision od MLEKOVITA wiązało się z zaprojektowaniem i wdrożeniem rozwiązania dla kontroli jakości na jednej z linii produkcyjnych. Finalnie, w toku udanej współpracy łącznie zainstalowaliśmy 6 systemów na 6 liniach produkcyjnych. Systemy zostały zaprojektowane w różnych konfiguracjach, w zależności od wymagań produkcyjnych danej linii. Każdy z nich został wyposażony w stację odrzutu produktów wadliwych.
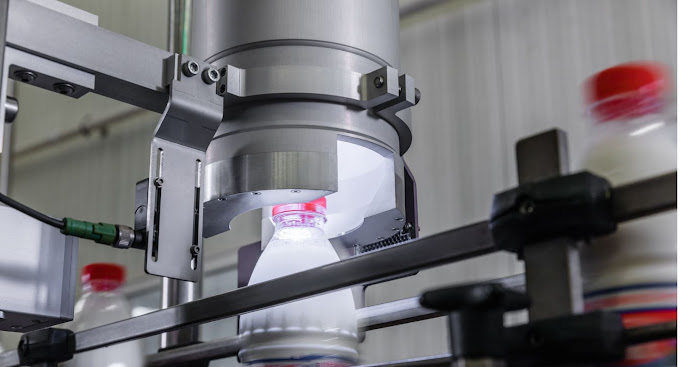
Co obejmowała inspekcja linii produkcyjnych w mleczarstwie systemami KSM Vision?
- Kontrolę nakrętek butelek PET i sprawdzenie poprawności zamknięcia.
- Kontrolę poziomu wlanego płynu (mleka, kefiru, jogurtu) do butelki
Wyzwania i zaproponowane rozwiązanie optymalizacji kontroli jakości
Zapewnienie poprawnej klasyfikacji (biorąc pod uwagę specyfikę produkcji taką jak: zróżnicowane kolory zakrętek, różnorodne kształty i wysokości opakowań) było ciekawym wyzwaniem.
Zadania nie ułatwiał też sam produkt: mleko bardzo się pieni, a naszym zadaniem było wyznaczenie poziomu płynu w butelce.
Aby walidacja produktów na liniach produkcyjnych przebiegała poprawnie:
- opracowaliśmy na potrzeby Klienta własną architekturę sieci neuronowej, która zapewnia odpowiednią wydajność i poziom klasyfikacji oraz umożliwia sterowanie czułością systemu za pomocą parametrów “tolerancji” dla każdej klasy.
- dzięki metodzie kalibracji głowic Inspect360+, a co za tym idzie danych, które na każdej z linii wyglądały tak samo, opracowaliśmy wspólny model sieci neuronowej.
- nie musieliśmy zmieniać formatu z poziomu graficznego interfejsu użytkownika, gdyż model sieci neuronowej sam rozpoznaje kolory nakrętek.
- zastosowaliśmy opatentowany zestaw zwierciadeł Inspect360+, który umożliwił obserwację góry oraz boków nakrętki z wykorzystaniem jednej kamery umieszczonej od góry.
- zainstalowaliśmy kamerę do badania poziomu nalania płynu razem z głowicą i odpowiednio dobranym oświetleniem, przez co rozwiązaliśmy problem kontroli nalanego mleka
- ułatwiliśmy procedurę zmiany wysokości głowicy w zależności od wysokości butelki poprzez “zafiksowanie” dwóch wysokości – minimalizując tym samym zaangażowanie operatorów linii produkcyjnej.
Warto wspomnieć też o rozwiązaniu ważnej dla Klienta kwestii “płynnej” klasyfikacji. Co to znaczy w praktyce? Dzięki płynnej klasyfikacji Klient ma możliwość ustawienia poziomu tolerancji zakrętek “dobrych” i “złych”:
- system umożliwia ustawienie dla każdej klasy paska tolerancji: jeśli w wyniku klasyfikacji zakrętka jest w 70% wadliwa, w 20% zabrudzona i na 10% dobra, operator może ustawić, że jeśli zakrętka jest dobra na 10% to uznajemy ją za dobrą, a jeśli jest dobra na < 10% to wtedy przydzielamy inne klasy.
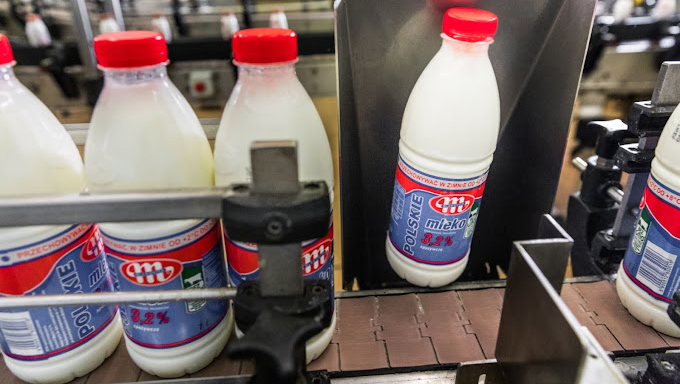
Dlaczego Grupa Mlekovita wybrała systemy kontroli jakości KSM Vision oparte sieciach neuronowych?
Pierwotnie planowane było wdrożenie naszych systemów tylko na jednej linii. Ostatecznie Klient zdecydował się na ich wdrożenie na pięciu innych. Dla każdej z nich zaprojektowaliśmy i wdrożyliśmy system dostosowany do wymagań konfekcjonowanych produktów:
- szerokie spektrum zastosowania: ruchoma głowica stacji kontrolnej Inspect360+, która umożliwia jej podnoszenie i opuszczanie, dopasowując do wysokości opakowania, a tym samym pozwalając na inspekcję różnych produktów.
- poprawa jakości klasyfikacji: dostosowaliśmy modele klasyfikacji do kolorów nakrętek występujących na danej linii:
- system rozróżnia te kolory i zapisuje w statystykach informacje, ile jakich produktów zostało wyprodukowanych,
- dodatkowo kamera sprawdza na górnej powierzchni nakrętki obecność nadruku daty przydatności do spożycia.
- wysoka wydajność i pełna kompatybilność naszych systemów kontroli z produkcją Klienta: linie działają z wydajnością do 12 000 szt/h.
- higiena i bezpieczeństwo: każdy z zainstalowanych systemów został wyposażony w stację odrzutu, skonstruowaną tak, aby nie przewracać odrzucanych butelek i ograniczyć ryzyko rozlania produktu na podłogę.
- możliwość klasyfikacji wad – tzn. system informuje nie tylko o fakcie nieprawidłowego zamknięcia, ale dostarcza dodatkowe informacje o defekcie (np. brak nakrętki, nakrętki uszkodzona, nakrętka zabrudzona).
- komunikacja: sygnalizator świetlny informuje o przepełnieniu stacji odrzutu i konieczności jej opróżnienia.
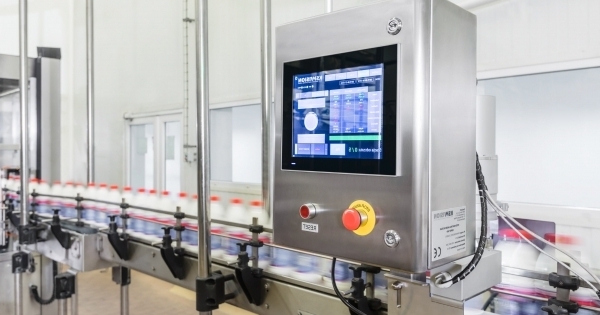
Co sprawia, że firmie produkującej produkty mleczarskie opłaca się i zwraca inwestycja w wizyjne systemy kontroli jakości?
Producent produktów mleczarskich powinien zainwestować w wizyjny system kontroli jakości z kilku ważnych powodów:
- Wykrywanie defektów: Wizyjne systemy potrafią precyzyjnie wykrywać wszelkie defekty, takie jak zanieczyszczenia, dziury, lub inne nieprawidłowości w produktach mleczarskich, co minimalizuje ryzyko dostarczenia wadliwych produktów na rynek.
- Utrzymanie jednolitej jakości: Dzięki ciągłej kontroli jakości, producent może utrzymać stałą jakość swoich produktów mleczarskich, co jest kluczowe dla zyskania i utrzymania zaufania klientów.
- Oszczędność czasu: Automatyczny proces wizyjnej kontroli jakości jest znacznie szybszy niż ręczna kontrola, co zwiększa wydajność produkcji.
- Redukcja strat: Eliminacja wadliwych produktów na wczesnym etapie produkcji pomaga w redukcji marnotrawstwa surowców i kosztów.
- Zgodność z regulacjami: Wizyjny system zapewnia, że produkty mleczarskie spełniają wszelkie przepisy i normy sanitarno-higieniczne.
- Minimalizacja ryzyka zdrowotnego: Wykrywanie potencjalnie szkodliwych zanieczyszczeń pozwala na uniknięcie ryzyka związanego z produktami niespełniającymi standardów zdrowotnych.
- Poprawa efektywności produkcji: Wizyjne systemy pozwalają na monitorowanie i optymalizację procesów produkcyjnych, co może prowadzić do oszczędności energii i surowców.
- Skrócenie czasu przestoju: W przypadku wykrycia problemu, wizyjny system może szybko uruchomić alarm, co pomaga w minimalizacji czasu przestoju linii produkcyjnej.
- Zwiększenie konkurencyjności: Stała kontrola jakości pozwala na dostarczanie klientom doskonałej jakości produktów, co może przekładać się na wyższe pozycjonowanie rynkowe.
- Budowanie reputacji: Inwestycja w wizyjny system kontroli jakości może przyczynić się do budowy pozytywnej reputacji producenta, co przyciąga klientów i zwiększa lojalność wobec marki.