Implementation of a vision quality control system in dairy industry

The path from one to 6 vision quality control systems installed on 6 production lines of the MLEKOVITA Group.
- The Mlekovita Group
- What did the inspection of dairy production lines with KSM Vision systems include?
- Challenges and suggested solutions for improving quality control
- Client's benefits, or why did Mlekovita choose our quality control systems based on neural networks?
- What makes it worthwhile and profitable for a dairy company to invest in vision-based quality control systems?
There is no development without well thought-out investments.
Dariusz Sapinski, President of the Management Board, MLEKOVITA Group
The Mlekovita Group
MLEKOVITA Group is the largest group of dairy companies in Central and Eastern Europe with over 90 years of tradition. The company exports its products to 167 countries around the world.
Initially, we were commissioned to design and implement a quality control solution on one of the production lines. In the end, the effective cooperation resulted in installation of the total of 6 systems on 6 production lines. The systems were designed in various configurations, depending on the production requirements of individual lines. Each system is equipped with defective product rejection stations.
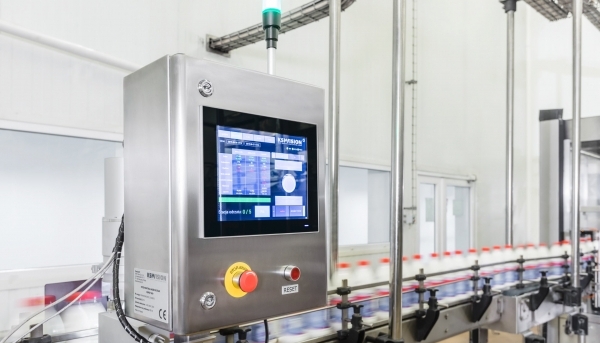
What did the inspection of dairy production lines with KSM Vision systems include?
- Inspection of the PET bottle caps and the correct closure.
- Inspection of the liquid level (milk, kefir, yoghurt) in the bottle.
Challenges and suggested solutions for improving quality control
Ensuring the correct classification (taking into account the specific nature of manufacturing process such as: different colours of caps, various shapes and heights of packages) was an interesting challenge.
What made the task even more difficult was the product itself: milk foams easily and our task was to determine the exact liquid level in the bottle.
In order to properly validate the products on production lines:
- We have developed our own neural network architecture for Customers, which ensures the appropriate performance and classification level and enables the system sensitivity to be controlled using “tolerance” parameters for each class.
- Thanks to the method of calibration of Inspect360+ heads, and thus the data, which looked the same on each line, we developed a common neural network model.
- We did not have to change the format from the level of graphical user interface, as the neural network model recognizes the cap colours itself.
- We used a patented set of Inspect360+ mirrors, which enables the observation of top and side surface of the cap with a single camera placed on the top.
- We installed a camera to test the poured liquid level together with a head and proper lighting, which solved the problem of controlling the fill level
- We have simplified the procedure of changing the head height depending on the bottle height by “fixing” two heights – thus minimizing the involvement of the production line operators.
Another thing that is worth mentioning is that we have solved the liquid classification problem, which is important for the Customer. What does that mean in practice? Thanks to the liquid classification, the Customer can set the tolerance margin for “good” and “bad” caps:
- the system allows you to set a tolerance margin for each class: if the classification says that the cap is 70% defective, 20% dirty and 10% good, the operator can using a setting that if the cap is 10% good then we consider it good, and if it is <10% good, we classify it differently.

Client's benefits, or why did Mlekovita choose our quality control systems based on neural networks?
As we mentioned at the beginning, our systems were originally planned to be implemented only on one line. In the end, the Customer decided to implement them on five other lines. For each of them, we designed and implemented a system tailored to the requirements of packaged products:
- A wide range of applications: the movable head of the Inspect360 + control station, which allows it to be raised and lowered, adjusting to the height of packaging, thus allowing the inspection of different products.
- Improved quality of classification: we have adjusted the classification models to the cap colours on individual lines
- The system recognizes those colours and records the statistics on the number of manufactured products,
- In addition, the camera checks if there is an expiration date stamp on the upper surface of the cap.
- High performance and full compatibility of our control systems with the Customer’s manufacturing process: the lines operate at a capacity of up to 12,000 psc/h.
- Safety and health: each installed system is equipped with a rejection station, so as not to knock over the rejected bottles and reduce the risk of spilling the product on the floor.
- Possible classification of defects, i.e. the system does not only alerts about improper closure, but also provides additional information about the defect (e.g. a missing cap, a damaged cap, a dirty cap).
- Communication: signal light informs you when the rejection station is full and needs emptying.
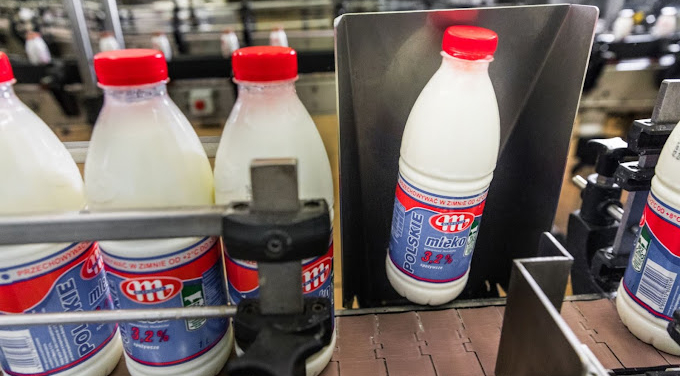
What makes it worthwhile and profitable for a dairy company to invest in vision-based quality control systems?
A dairy producer should invest in a vision-based quality control system for several important reasons:
- Defect detection: Vision-based systems can accurately detect any defects, such as contaminants, holes, or other irregularities in dairy products, minimizing the risk of defective products reaching the market.
- Maintaining consistent quality: With continuous quality control, a manufacturer can maintain consistent quality in its dairy products, which is key to gaining and maintaining customer confidence.
- Time savings: The automated vision quality control process is much faster than manual inspection, increasing production efficiency.
- Loss reduction: Eliminating defective products early in production helps reduce wasted raw materials and costs.
- Regulatory compliance: A vision-based system ensures that dairy products meet all regulations and health and hygiene standards.
- Minimizing health risks: Detection of potentially harmful contaminants avoids risks associated with products that do not meet health standards.
- Improving production efficiency: Vision-based systems allow monitoring and optimization of production processes, which can lead to savings in energy and raw materials.
- Reducing downtime: When a problem is detected, the vision system can quickly sound an alarm, helping to minimize production line downtime.
- Increased competitiveness: Constant quality control allows you to deliver excellent quality products to your customers, which can translate into higher market positioning.
- Building reputation: Investing in a vision-based quality control system can help build a positive reputation for a manufacturer, which attracts customers and increases brand loyalty.