Wyzwanie związane z niewłaściwym oznakowaniem w branży FMCG: statystyki, przyczyny, konsekwencje i… rozwiązania
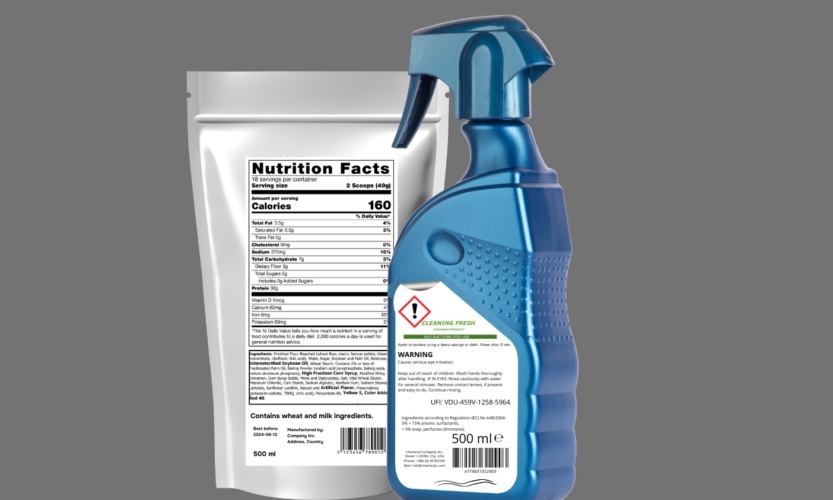
Od składników i alergenów po daty ważności – etykiety są kluczowe w przekazywaniu istotnych informacji konsumentom, zapewnianiu bezpieczeństwa produktów i utrzymywaniu integralności marki. Mimo to incydenty związane z błędnym etykietowaniem nadal stanowią poważne wyzwanie dla producentów, zwłaszcza globalnych firm z sektora FMCG eksportujących swoje towary. Gdy całe kontenery lub partie produktów bywają wycofywane z rynku (i najczęściej utylizowane) z powodu błędów na etykietach, nie sposób przecenić znaczenia prawidłowego znakowania opakowań. Dlaczego problem błędów na etykietach w ogóle wciąż występuje w dobie zautomatyzowanej kontroli jakości?
- Statystyki wycofywania produktów z rynku w związku z błędnym etykietowaniem
- Zwroty produktów na świecie z powodu niewłaściwego etykietowania - dane za: lipiec 2024
- Zwroty produktów w UE z powodu niewłaściwego etykietowania - dane od połowy sierpnia do połowy września 2024, UE
- Przyczyny błędnego etykietowania w produkcji FMCG
- Konsekwencje błędów na etykietach
- Automatyzacja i Digitalizacja jako Rozwiązania dla Błędów Etykietowania
- Dlaczego w dobie automatyzacji kontroli jakości etykiet dane o zwrotach z powodu błędów wciąż są wysokie?
- Inspect 360+ LI RS produkcji KSM Vision: Unikatowe rozwiązanie do automatyzacji kontroli jakości etykietowania
- Pracujesz w produkcji FMCG i potrzebujesz więcej informacji lub wsparcia w doborze systemu kontroli jakości?
W globalnym sektorze dóbr szybko zbywalnych (FMCG) błędne etykietowanie pozostaje kluczowym i złożonym problemem. Brak składników lub alergenów na etykiecie? Niewłaściwy język? Zła data ważności? Etykiety pełnią fundamentalną rolę w przekazywaniu istotnych informacji konsumentom, zapewnianiu bezpieczeństwa produktów oraz utrzymaniu integralności marki. Jak to możliwe, że w erze sztucznej inteligencji, automatyzacji i robotyki w fabrykach problem błędnego etykietowania nadal występuje, przynosząc znaczące konsekwencje dla producentów, konsumentów i środowiska? Przyjrzyjmy się bliżej temu zagadnieniu, analizując liczby.
Statystyki wycofywania produktów z rynku w związku z błędnym etykietowaniem
Najnowsze dane dotyczące kontroli jakości etykiet ujawniają alarmujące statystyki związane z błędnym etykietowaniem. Dokładne oznakowanie jest kluczowe nie tylko dla zaufania konsumentów, ale również dla zgodności z przepisami prawnymi, ponieważ błędne etykiety mogą stanowić poważne zagrożenie dla zdrowia. W samej branży spożywczej około 40% odrzuceń produktów w regionach takich jak UE i USA wynika z niewłaściwego etykietowania żywności, a 30% wycofań produktów spowodowane jest niezadeklarowanymi alergenami. Te dane podkreślają ogromne wyzwanie i pilność utrzymania rygorystycznych standardów etykietowania przez producentów.
Poniżej znajdują się szczegółowe dane rynkowe dotyczące wycofań produktów z powodu błędów w etykietowaniu.
Źródła:
IFS certification
European Commission
Zwroty produktów na świecie z powodu niewłaściwego etykietowania - dane za: lipiec 2024
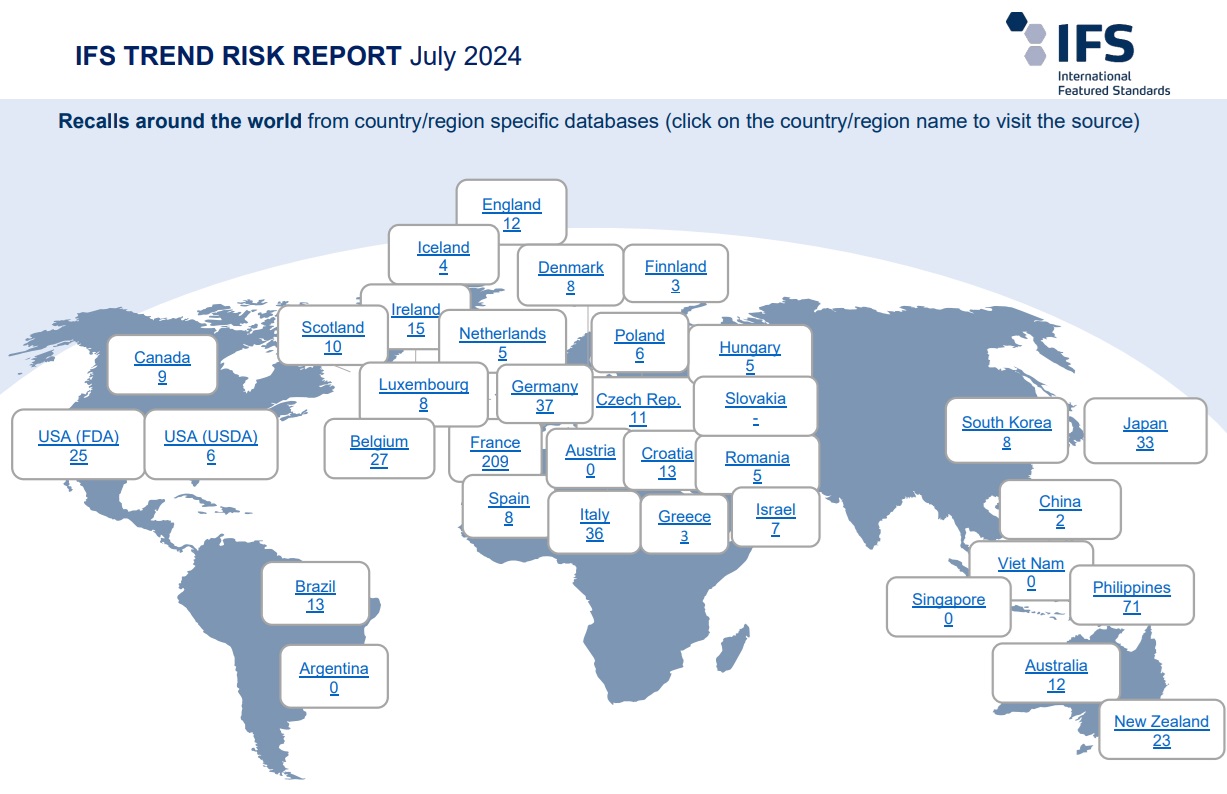
Zwroty produktów w UE z powodu niewłaściwego etykietowania - dane od połowy sierpnia do połowy września 2024, UE
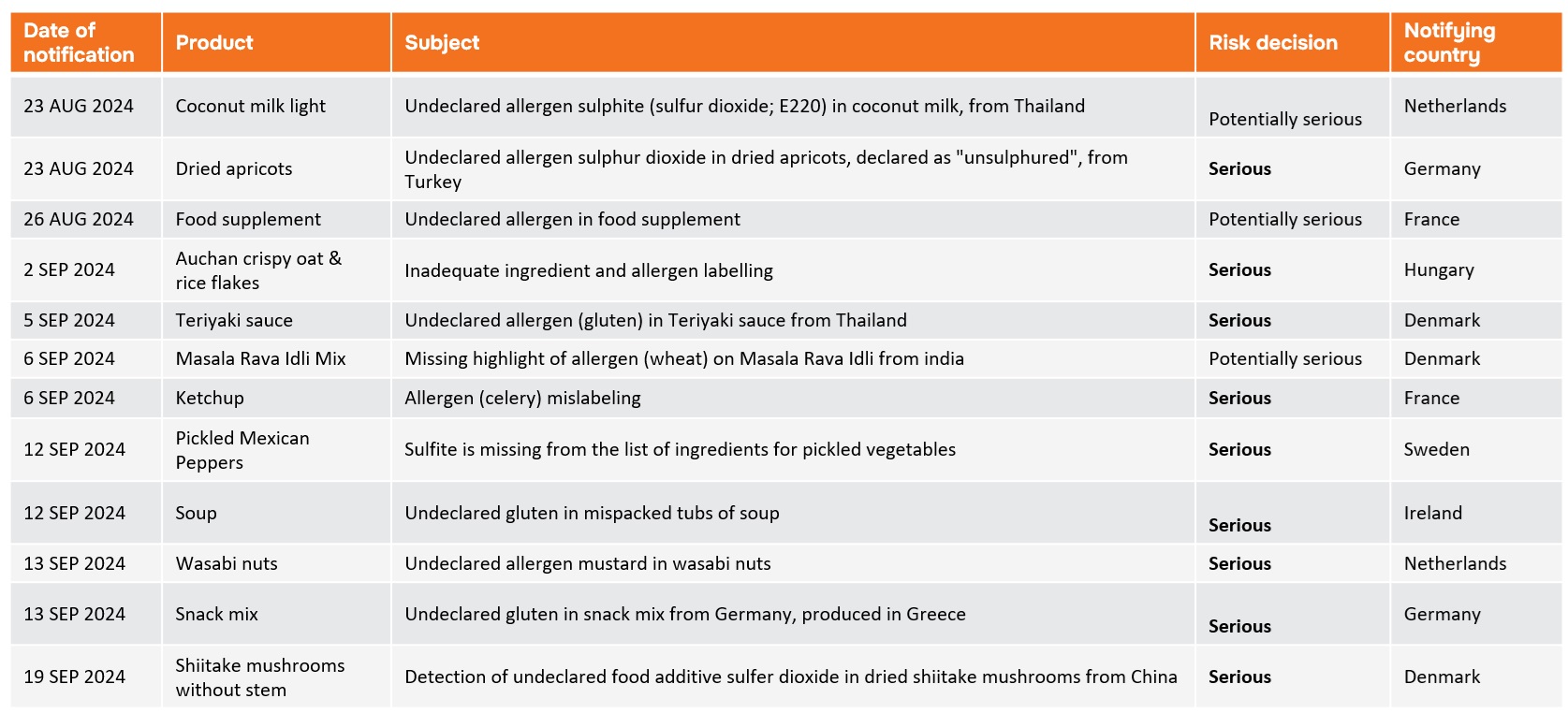
Przyczyny błędnego etykietowania w produkcji FMCG
Błędne etykietowanie produktów FMCG może wynikać z kilku czynników, w tym błędów ludzkich, niewystarczającego poziomu kontroli jakości, złożoności łańcucha dostaw oraz nieefektywnych procesów etykietowania. Najważniejsze przyczyny błędów na etykietach w procesie produkcyjnym:
-
Błędy ludzkie
Mimo rosnącego wykorzystania systemów automatyzacji, wiele zadań związanych z etykietowaniem nadal opiera się na pracy ludzkiej. Obecnie systemy kontroli jakości w inspekcji opakowań są często ręcznie konfigurowane przez operatorów bezpośrednio na linii produkcyjnej, co prowadzi do błędów ludzkich i potencjalnych przestojów. Do błędów może dochodzić z różnych powodów, takich jak zmęczenie, brak odpowiedniego szkolenia czy zwykłe przeoczenie. W przypadku globalnych producentów FMCG eksportujących towary na rynki o odmiennych wymaganiach prawnych dotyczących etykietowania, błędy na etykietach mogą pojawiać się łatwiej i częściej. Gdy pracownik niewłaściwie oznakuje partię, błąd może pozostać niezauważony aż do momentu, gdy cały produkt zostanie wyprodukowany, dotrze za granicę, a w najgorszym scenariuszu – trafi na półkę sklepową do konsumentów.
-
Złożoność wymogów etykietowania
Branża FMCG boryka się ze skomplikowanymi wymogami dotyczącymi etykietowania, szczególnie w przypadku produktów spożywczych, napojów, kosmetyków, chemii czy farmaceutyków. Przepisy te różnią się w zależności od regionu i często ulegają zmianom w wyniku nowych odkryć naukowych lub zmian w regulacjach. Producenci mogą mieć trudności z nadążaniem za tymi wymogami, co prowadzi do niezamierzonych błędów na etykietach. Złożoność problemu rośnie wraz z międzynarodową dystrybucją, ponieważ produkty wymagają lokalizacji etykiet, aby spełnić regulacje specyficzne dla poszczególnych krajów.
-
Supply Chain Complexity and Communication Gaps
Współczesne łańcuchy dostaw są rozległe i obejmują wielu interesariuszy – od dostawców surowców, przez dostawców opakowań, aż po sieci dystrybucji. Luki komunikacyjne w tej złożonej sieci mogą skutkować zastosowaniem nieprawidłowych informacji na etykietach. Na przykład, jeśli dostawca składników zmieni skład surowca, ale nie powiadomi o tym na czas producenta, etykieta końcowego produktu może nie zawierać prawidłowych informacji, co stwarza ryzyko błędnego oznakowania alergenów i zagraża bezpieczeństwu konsumenta.
Szybkie cykle produkcyjne często wywierają presję na producentów produkcji wysokowydajnej, aby przesuwać produkty w szybkim tempie na linii produkcyjnej. Jednak ta presja może prowadzić do pośpiesznych procesów i błędów. Etykiety mogą być niewłaściwie nakładane lub drukowane z błędami podczas tych operacji o wysokiej prędkości. Co więcej, przestarzały sprzęt lub brak zsynchronizowanych systemów w całej linii produkcyjnej mogą zwiększać ryzyko błędnego etykietowania.
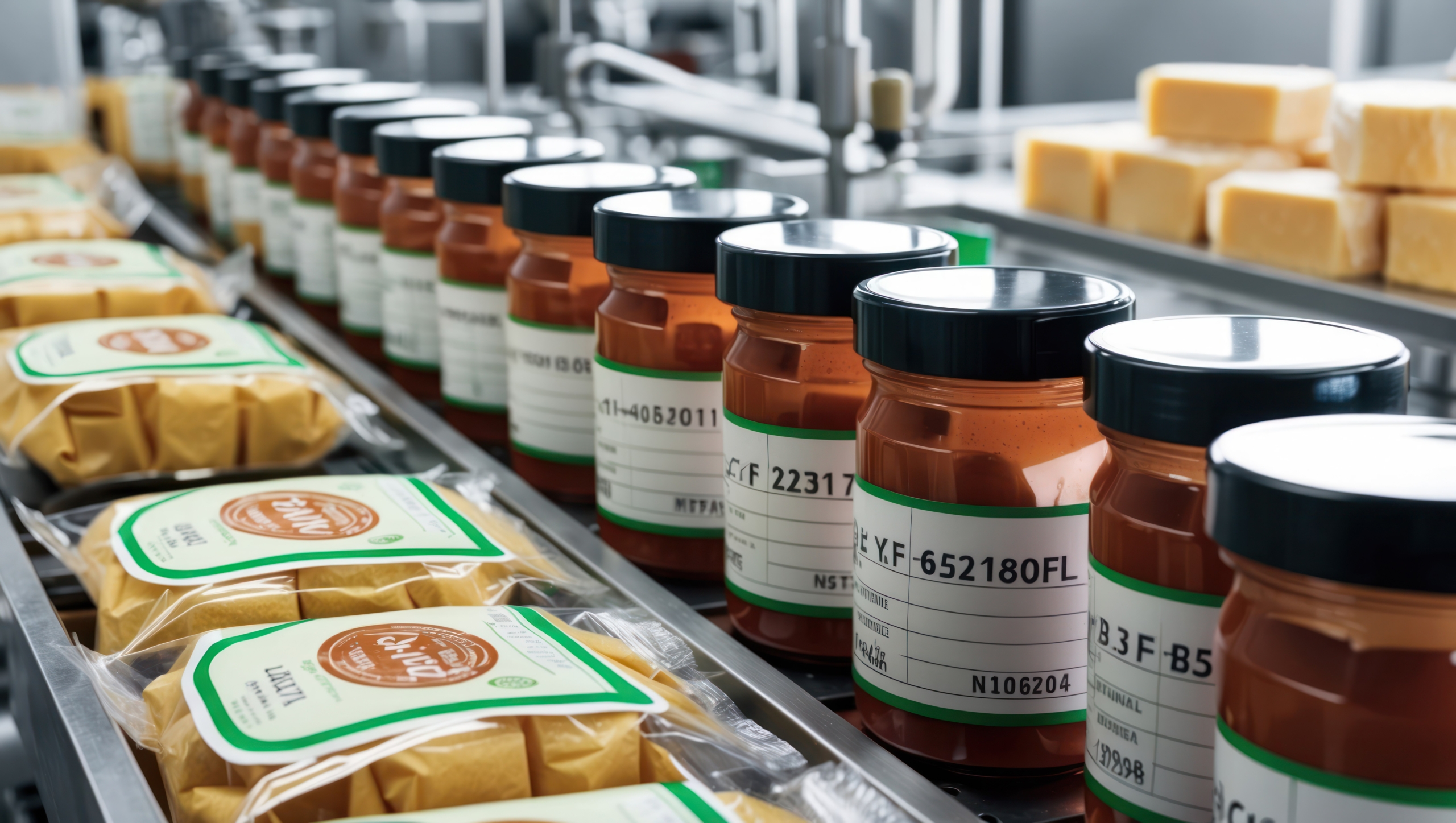
Konsekwencje błędów na etykietach
Błędne etykietowanie ma daleko idące konsekwencje, które dotykają nie tylko producentów, ale także konsumentów, organy regulacyjne i środowisko.
-
Straty finansowe i operacyjne związane z wycofaniem lub zwrotami produktów
Dla producentów z sektora FMCG błędne etykietowanie może prowadzić do znacznych strat finansowych i operacyjnych. Koszty związane z wycofaniem błędnie oznakowanych produktów z rynku obejmują wydatki logistyczne, opłaty za utylizację produktów oraz rekompensaty dla sprzedawców detalicznych. Duże akcje wycofania często oznaczają usunięcie całych partii lub kontenerów , co prowadzi do strat sięgających milionów dolarów. Dodatkowo, takie wycofania zakłócają łańcuchy dostaw, wpływając na terminy dostaw i relacje z dostawcami oraz sprzedawcami.
-
Utrudnienie realizacji celów zrównoważonego rozwoju i wpływ na środowisko
Błędne etykietowanie może prowadzić do działań prawnych i kar finansowych. W regionach takich jak Unia Europejska i Stany Zjednoczone obowiązują surowe przepisy dotyczące etykietowania, które wymagają pełnego ujawnienia składników, alergenów i dokładnych opisów produktów. Organy regulacyjne często nakładają grzywny na producentów za nieprzestrzeganie tych standardów. W niektórych przypadkach poważne naruszenia mogą prowadzić do zakazu lub ograniczeń sprzedaży produktów, zwłaszcza jeśli błędy w etykietowaniu występują wielokrotnie.
-
Konsekwencje prawne i regulacyjne
Błędne etykietowanie często skutkuje wycofaniem całych kontenerów lub partii produktów z rynku i ich utylizacją, nawet jeśli same produkty są bezpieczne do spożycia lub użycia. Prowadzi to do ogromnego marnotrawstwa zasobów, w tym materiałów opakowaniowych, etykiet oraz samych produktów. W przypadku artykułów spożywczych błędne etykietowanie przyczynia się do marnotrawstwa żywności, pogłębiając globalny kryzys związany z bezpieczeństwem żywnościowym. Dodatkowo, utylizacja tych produktów zwiększa ilość odpadów trafiających na wysypiska i emisję dwutlenku węgla. W ten sposób błędy związane z etykietowaniem, wynikające z ręcznych błędów czy awarii, utrudniają realizację celów automatyzacji, cyfryzacji i zrównoważonego rozwoju oraz przestrzeganie zasad zero waste i regulacji proekologicznych, którym obowiązują producentów wysokonakładowych.
-
Ryzyko dla zdrowia konsumentów
Błędne etykietowanie stanowi bezpośrednie zagrożenie dla zdrowia konsumentów, szczególnie w przypadkach błędnych informacji o alergenach, wartościach odżywczych lub datach ważności – dotyczy to zwłaszcza przemysłu spożywczego, produkcji napojów (w tym alkoholu), produktów farmaceutycznych i kosmetyków. Dla osób z alergiami spożycie produktu zawierającego nieujawnione alergeny może mieć poważne, a nawet śmiertelne konsekwencje. Nieprawidłowe daty ważności mogą prowadzić do spożycia zepsutej żywności, co stwarza zagrożenie dla zdrowia, natomiast błędne informacje o dawkowaniu w produktach farmaceutycznych mogą prowadzić do przedawkowania lub nieskutecznego leczenia.
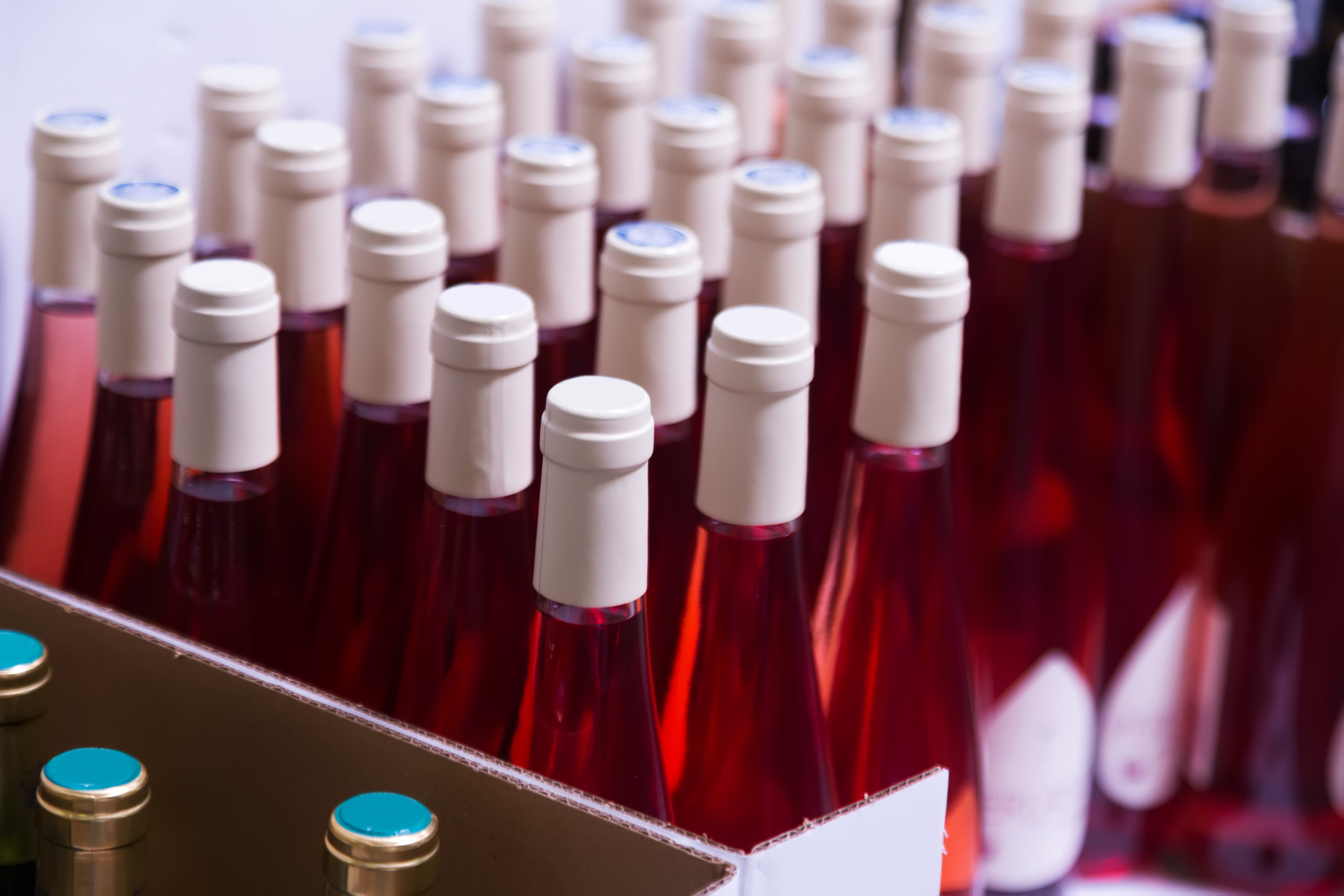
Automatyzacja i Digitalizacja jako Rozwiązania dla Błędów Etykietowania
W obliczu rosnącego problemu błędnego etykietowania wielu producentów zwraca się ku automatyzacji i cyfryzacji, aby zwiększyć precyzję oznakowania oraz zmniejszyć ryzyko błędów ludzkich. Szczególnie systemy wizyjne stanowią potężne narzędzie do kontroli jakości, znacznie podnosząc dokładność etykietowania w środowiskach produkcyjnych o wysokiej wydajności.
Jak działa zautomatyzowana wizja maszynowa?
Systemy wizyjne do kontroli jakości etykiet wykorzystują przemysłowe kamery o wysokiej rozdzielczości, zaawansowane oprogramowanie oraz algorytmy sztucznej inteligencji, w czasie rzeczywistym kontrolujące jakość etykiety produktów poruszających się na linii produkcyjnej. Poprzez rejestrowanie obrazów etykiet i porównywanie ich z szablonami referencyjnymi, systemy te mogą identyfikować nawet najmniejsze niezgodności, defekty takie jak nieprawidłowy tekst, brakujące elementy czy błędy w wyrównaniu. Technologia wizji maszynowej może również skanować kody kreskowe, kody QR oraz inne znaczniki identyfikacyjne, aby upewnić się, że każdemu produktowi przypisana jest odpowiednia etykieta.
Po wykryciu błędu system oznacza wadliwy produkt, często kierując go z linii produkcyjnej przed etapem pakowania lub wysyłki. Systemy te można skonfigurować do inspekcji dużej liczby produktów z ogromną prędkością, co sprawia, że są one niezwykle efektywne w produkcji na dużą skalę. Systemy wizyjne śledzą również dane z inspekcji, co pozwala identyfikować powtarzające się problemy lub wzorce, umożliwiając producentom wprowadzanie korekt procesów, by zredukować błędy w etykietowaniu w dłuższej perspektywie. Dzięki automatyzacji kontroli jakości systemy wizyjne znacząco zmniejszają zależność od ludzkich inspektorów, redukując ryzyko błędów ludzkich i zwiększając ogólną precyzję etykietowania.
Rzeczywisty przykład?
Przykładem systemu wizyjnego do automatycznej kontroli jakości etykiet jest Inspect 360+ LI firmy KSM Vision.
Elastyczność Inspect 360+ LI pozwala na zastosowanie systemu do różnych formatów:
- opakowania: butelki z atomizerem, kartony, saszetki, torby, doypacki, worki instant, bigbagi, tacki, saszetki, butelki o nietypowych kształtach i zagięciach
- etykiety: papierowe, z folii typu sleeve
Inspect 360+ LI zapewnia pełną automatyczną detekcję potencjalnych defektów etykiet, obejmującą inspekcję i analizę takich elementów jak:
- kody serii produkcyjnej (BATCH), EAN, UFI
- obecność etykiety
- pozycja i lokalizacja etykiety na opakowaniu
- odwrócona lub obrócona etykieta
- przesunięcie etykiety
- odklejanie się
- zmarszczenia
- nakładanie się etykiet
- niewyraźny druk, rozmyta grafika, itp.
Dla saszetek, opakowań typu pouch, torebek z zamkiem błyskawicznym, posiłków „instant” itp., Inspect 360+ LI dodatkowo przeprowadza inspekcję uszczelnień:
- rozmyty tekst
- wysokość produktu
- szczelność
- uszczelnienie górne/boczne
- ubytki (np. w opakowaniach typu pouch)
- deformacje
- brak ciągłości uszczelnienia
- obecność ciał obcych (zwykle małe fragmenty zapakowanej żywności)
Inspect 360+ LI jest dostosowany do wymogów korporacyjnych w zakresie systemów IT zakładu produkcyjnego, w tym do wymiany danych, zarządzania uprawnieniami użytkowników oraz raportowania.
Dlaczego w dobie automatyzacji kontroli jakości etykiet dane o zwrotach z powodu błędów wciąż są wysokie?
Znaczenie właściwego oznakowania produktów na współczesnym rynku FMCG (dóbr szybkozbywalnych) nie może być przecenione. Mimo to, dane przytoczone wcześniej w artykule wskazują, że liczba wycofań produktów z rynku z powodu błędnego oznakowania wciąż jest wysoka. Co utrudnia zapewnienie zgodności etykiet w produkcji?
-
Wysoki koszt początkowy inwestycji w system wizyjny
Z jednej strony wdrożenie systemów wizyjnych i zautomatyzowanych rozwiązań do etykietowania wymaga znacznych nakładów początkowych na technologię, infrastrukturę oraz szkolenie pracowników. Koszty te mogą być zaporowe dla małych i średnich producentów, choć długofalowo mogą oni znacznie skorzystać na redukcji błędów oraz zwiększeniu efektywności operacyjnej.
Z tego powodu istotne jest, aby wybrać producenta systemów wizyjnych (OEM), który oferuje rozwiązania z krótkim okresem zwrotu z inwestycji. W przypadku systemów wizyjnych KSM Vision, okres zwrotu może wynosić zaledwie 12 miesięcy.
-
Integracja z istniejącymi systemami i infrastrukturą
-
Ręczna konfiguracja systemów wizyjnych przez operatorów
Kolejnym istotnym czynnikiem wpływającym na ograniczoną wydajność systemów wizyjnych w zakresie kontroli prawidłowości etykietowania jest fakt, że obecnie systemy kontroli jakości opakowań są ręcznie konfigurowane przez operatorów na linii produkcyjnej, co pozwala na popełnianie błędów ludzkich. Obecne rozwiązania na rynku wymagają ręcznej obsługi, zwłaszcza w zakresie kalibracji i parametryzacji dla nowych formatów i produktów..
Rozwiązanie dla wyzwań producentów związanych z automatyzacją kontroli jakości etykiet?
To wyzwanie produkcyjne nie zostało jak dotąd rozwiązane przez żaden OEM („Original Equipment Manufacturer”)… aż do teraz. Firma KSM Vision podjęła się opracowania „w pełni zautomatyzowanego i samokalibrującego systemu inspekcji jakości etykiet” we współpracy z Campden BRI Hungary i Maspex przy wsparciu Europejskiego Instytutu Innowacji i Technologii (EIT Food). Projekt badawczo-rozwojowy KSM Vision obejmuje proces automatyzacji i digitalizacji testowania jakości etykiet w celu zminimalizowania marnotrawstwa produkcji spowodowanego błędami na etykietach produktów spożywczych. Innowacyjny system inspekcji jakości etykiet, opracowany w ramach projektu R&D, zapewni „w pełni zautomatyzowaną kontrolę produktów na liniach produkcyjnych”, co uprości procedurę kontroli jakości i przyczyni się do redukcji odpadów w sektorze FMCG – w tym przypadku z naciskiem na transformację ekologiczną w przemyśle spożywczym.
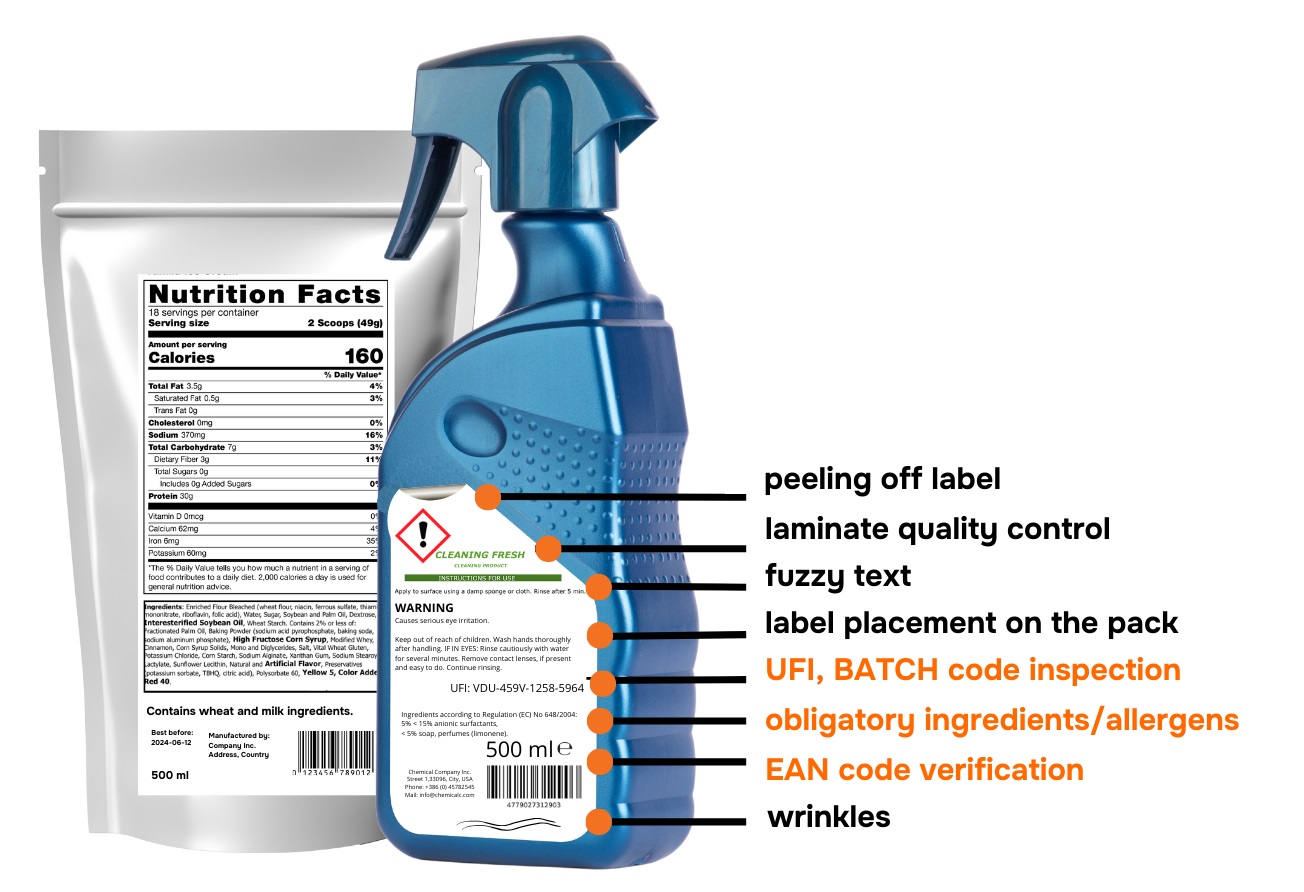
Inspect 360+ LI RS produkcji KSM Vision: Unikatowe rozwiązanie do automatyzacji kontroli jakości etykietowania
Pracujesz w produkcji FMCG i potrzebujesz więcej informacji lub wsparcia w doborze systemu kontroli jakości?
W KSM Vision specjalizujemy się w rozwiązaniach automatyzacji kontroli jakości, które dzięki zaawansowanym detektorom sztucznej inteligencji (w tym deep learning AI) i technologiom widzenia maszynowego skutecznie zastępują ręczną inspekcję, znacznie poprawiając zarówno dokładność, jak i efektywność kosztową.
Oferujemy unikatowe połączenie algorytmów uczenia maszynowego z indywidualnie zaprojektowanym sprzętem, w pełni zintegrowanym z istniejącymi liniami produkcyjnymi i systemami IT (wymiana danych, uprawnienia, raportowanie), zapewniając płynne działanie i pełną kompatybilność.
Nasze zindywidualizowane podejście pozwala nam dostosować nasze rozwiązania do konkretnych potrzeb i wyzwań związanych z inspekcją zakładu/produktu, umożliwiając nam skuteczne spełnianie wymagań korporacyjnych. Jest to kluczowy wyróżnik KSM Vision na tle innych producentów OEM.
Czy stoisz w obliczu nierozwiązanych problemów z defektami lub którykolwiek z Twoich procesów produkcyjnych nadal opiera się na kontroli ręcznej? Zapraszamy do kontaktu z naszymi inżynierami pod adresem zapraszamy@ksmvision.com, aby podzielić się swoimi wyzwaniami produkcyjnymi. Przeanalizujemy wyzwania, przed którymi stoi Twój zakład produkcyjny, dostarczymy jak najwięcej know-how w dziedzinie automatyzacji i wizji maszynowej (bez względu na dostawcę rynkowego doradzimy najlepsze rozwiązanie do specyfiki Twojej linii produkcyjnej i produktów) i ustalimy, czy niestandardowe rozwiązania KSM Vision mogą sprostać Twoim wyzwaniom.