Inspect 360+ DSC
Compact system
for automated 360°
machine vision control
of empty cans
without dead angles
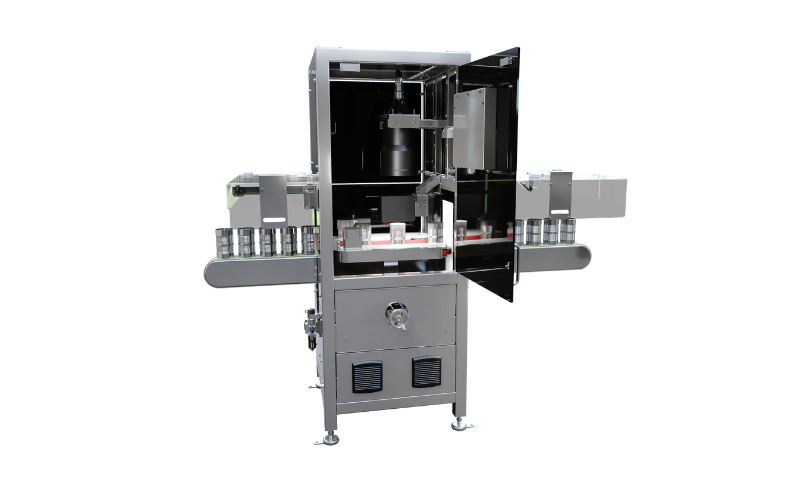
- About
- Advantages
- Defects detected
- Technical Data
- Gallery
- Brochure
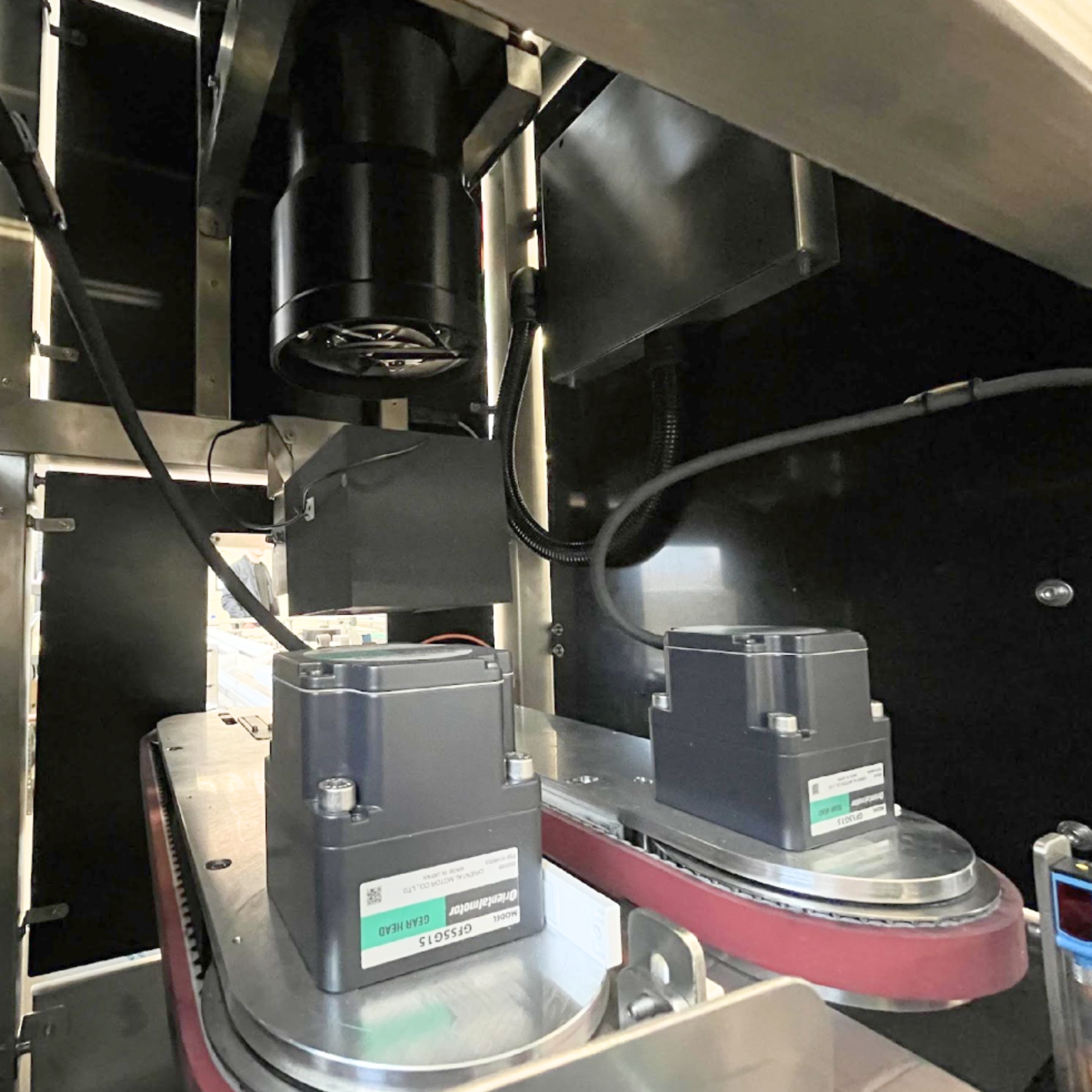
The innovative Inspect 360+ DSC optical system is an advanced automation with software based on the machine learning. Using deep neural networks, the system can eliminate manual inspection of products, increasing inspection efficiency.
The system is customized to meet corporate requirements for manufacturing plant IT systems: data exchange, user rights management, reporting.
Inspect 360+ DSC meets GUPH hygiene standards and HACCP guidelines, as well as the requirements of advanced production lines with fast continuous motion (high-volume production).
The head with a telecentric lens inspects the rim of the can, the bottom and the side walls.
An orthogonal view of the can is generated, enabling uniform inspection accuracy of the entire can, without perspective error.
The flexibility of Inspect 360+ DSC systems allows for customization of product formats, including:
- aluminum and steel cans
- 2- and 3-piece cans
- open and closed cans (2 independent systems)
The system is customized to meet corporate requirements for manufacturing plant IT systems: data exchange, user rights management, reporting.
Inspect 360+ DSC meets GUPH hygiene standards and HACCP guidelines, as well as the requirements of advanced production lines with fast continuous motion (high-volume production).
The head with a telecentric lens inspects the rim of the can, the bottom and the side walls.
An orthogonal view of the can is generated, enabling uniform inspection accuracy of the entire can, without perspective error.
The flexibility of Inspect 360+ DSC systems allows for customization of product formats, including:
- aluminum and steel cans
- 2- and 3-piece cans
- open and closed cans (2 independent systems)
Advantages:
- compliance with GUPH hygiene standards and HACCP guidelines
- compact head design takes up less space on the production line (1 camera with telecentric system)
- homogeneous inspection accuracy, without perspective error
- possibility of installation on high-speed production lines (capacity up to 30,000 containers per hour)
- integration with production plant IT systems for: data exchange, user rights management, reporting
- easy installation on new and existing production lines
- user-friendly interface to quickly add products and create a new order (in visual form)
- automated formatting of the system's mechanical components under new can formats
- 100% production control - only defect-free products leave production
- centralized qualitative and quantitative product control
Options:
- separation system (wedge conveyor)
- separation system (multi-segment rejecter)
- detection of imprints on the can - code, BATCH#, expiration date, logo
- defined trend values and alarms
- detailed reporting
- automatic head alignment (X, Y axis) to a new order
What do you gain?
- guaranteed consumer safety
- solving labor shortages by introducing automated machine vision based on artificial intelligence in place of manual inspection
- enhancement of brand reputation and trust - consistent delivery of high quality products
- avoiding problems and costs in the downstream process (return of a packing slip, whole batch, container, etc.)
- compliance with GUPH hygiene standards and HACCP guidelines
- compact head design takes up less space on the production line (1 camera with telecentric system)
- homogeneous inspection accuracy, without perspective error
- possibility of installation on high-speed production lines (capacity up to 30,000 containers per hour)
- integration with production plant IT systems for: data exchange, user rights management, reporting
- easy installation on new and existing production lines
- user-friendly interface to quickly add products and create a new order (in visual form)
- automated formatting of the system's mechanical components under new can formats
- 100% production control - only defect-free products leave production
- centralized qualitative and quantitative product control
Options:
- separation system (wedge conveyor)
- separation system (multi-segment rejecter)
- detection of imprints on the can - code, BATCH#, expiration date, logo
- defined trend values and alarms
- detailed reporting
- automatic head alignment (X, Y axis) to a new order
What do you gain?
- guaranteed consumer safety
- solving labor shortages by introducing automated machine vision based on artificial intelligence in place of manual inspection
- enhancement of brand reputation and trust - consistent delivery of high quality products
- avoiding problems and costs in the downstream process (return of a packing slip, whole batch, container, etc.)
The system provides full control of the open can including the rim, flange and sidewalls. Detection includes:
- mechanical damage - dents
- kinks, micro-holes, dents
- ellipticity
- scratches, folds
- color (dark stains, rust)
- impurities - foreign bodies or inclusions on the rim
- diameter errors
- deformations
(optional)
- imprints on cans - BATCH#, expiration date, logo
- mechanical damage - dents
- kinks, micro-holes, dents
- ellipticity
- scratches, folds
- color (dark stains, rust)
- impurities - foreign bodies or inclusions on the rim
- diameter errors
- deformations
(optional)
- imprints on cans - BATCH#, expiration date, logo
The system includes the following components:
- measuring head with 1 camera with telecentric system, dedicated LED lighting
- user-friendly touch panel - allowing controlling machine operation
- dedicated controller allowing integration with the control logic of the production line
- assembly components for the production line
- reject station (optional)
- automatic head height adjustment system (optional)
Configurable interface and database
Based on the production specification system interface can be adjusted, including automatic system set-up with data upload by higher-order system (e.g. MES) and additional data upload by line operator. Data collected by the system can be automatically uploaded to higher-order system.
- measuring head with 1 camera with telecentric system, dedicated LED lighting
- user-friendly touch panel - allowing controlling machine operation
- dedicated controller allowing integration with the control logic of the production line
- assembly components for the production line
- reject station (optional)
- automatic head height adjustment system (optional)
Configurable interface and database
Based on the production specification system interface can be adjusted, including automatic system set-up with data upload by higher-order system (e.g. MES) and additional data upload by line operator. Data collected by the system can be automatically uploaded to higher-order system.
They trust our know-how:
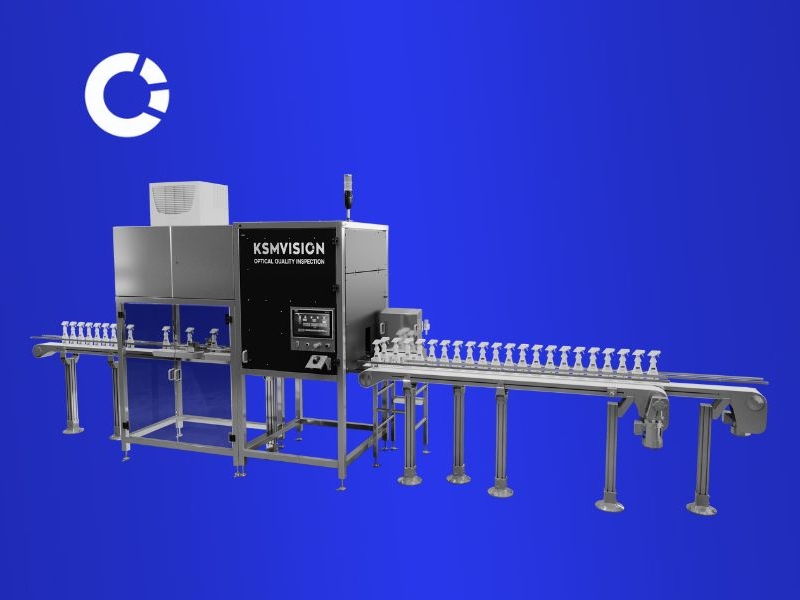