Inspect 360+ CL
Unique, compact
head with a set of mirrors
allows 360° inspection of
caps and lids
bottles and vials
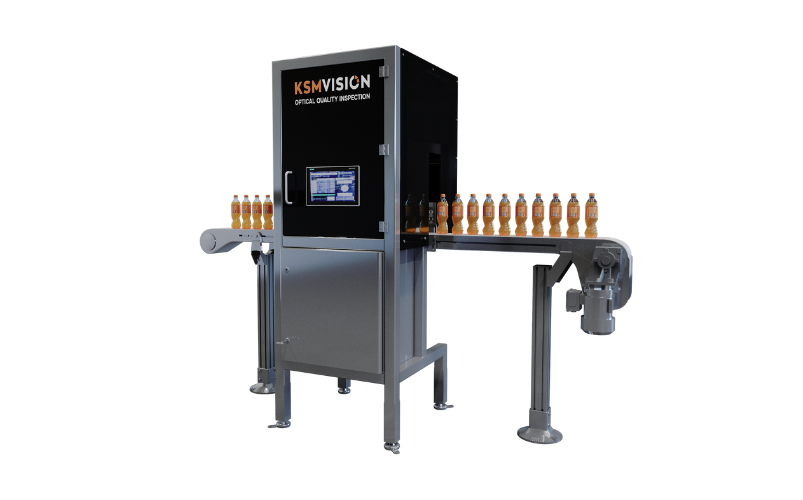
- About
- Advantages
- Defects detected
- Technical Data
- Gallery
- Brochure
- Concept
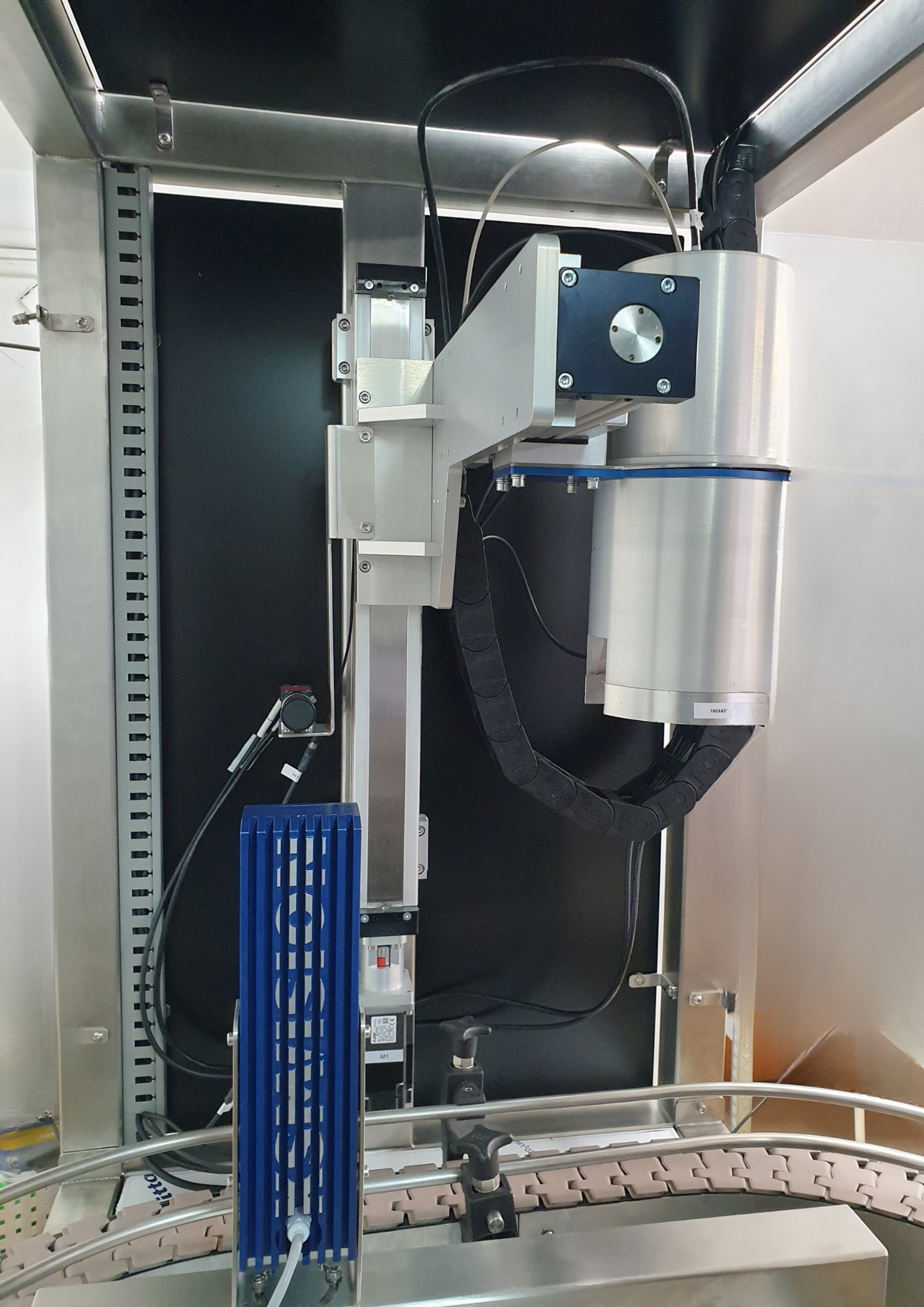
The innovative Inspect 360+ CL advanced automated optics system uses machine learning algorithms to run the quality control of various cap closures. It is used on high-volume production lines used for filling / sealing vials, bottles and other similar containers.
A distinguishing feature of the system is its compact, smart design. The innovative design - a head with only 1 camera and a set of mirrors allowing simultaneous 360° observation including side and bottom surfaces (KSM Vision PL Patent No. 229618) - provides an intuitive and functional system design, which allows easy and fast integration into existing production lines in a non-invasive way.
Using neural networks, the system can eliminate manual inspection of products, increasing inspection efficiency. It is customized to meet corporate requirements for manufacturing plant IT systems: data exchange, user rights management, reporting.
Using neural network architecture, it takes less than 5 minutes to train the system for new product formats.
Inspect 360+ CL provides circumferential 360° inspection of various types of caps, caps and other liquid packaging closures (bottles, vials, etc.). It enables automatic detection of defects in closures, such as, among others: deformations, wrinkles, unscrewing, creases, cracks, discoloration, skewing. It also distinguishes color, and as an option, the system enables analysis of imprints on closures, such as logos, expiration date, BATCH #, QR code.
A great advantage of the system is the ability to image the bottom surface of the cap put on vials, which are used in the production of antibiotics or vaccines (high-margin products) closed in vials.
Optionally, Inspect 360+ CL offers the fill level control. The fill level control module enables the operator setting the required parameters and the permissible margin of error via intuitive touch panel. Based on the given data, the system detects differences in the liquid fill level.
The system meets the requirements of advanced production lines with fast continuous motion (high-volume production).
The Inspect 360+ CL series are a machine vision systems tailored for the cosmetic, pharmaceutical, food industries, and more broadly FMCG.
Learn more about quality control automation per industry:
- quality control vision systems for manufacturers of cosmetics
- quality control vision systems for manufacturers of food and beverage
- quality control vision systems for manufacturers of pills and supplements
Check other KSM Vision's vision systems for your industry:
- machine vision for cosmetic industry by KSM Vision
- machine vision for food industry by KSM Vision
- machine vision for pharma industry by KSM Vision
A distinguishing feature of the system is its compact, smart design. The innovative design - a head with only 1 camera and a set of mirrors allowing simultaneous 360° observation including side and bottom surfaces (KSM Vision PL Patent No. 229618) - provides an intuitive and functional system design, which allows easy and fast integration into existing production lines in a non-invasive way.
Using neural networks, the system can eliminate manual inspection of products, increasing inspection efficiency. It is customized to meet corporate requirements for manufacturing plant IT systems: data exchange, user rights management, reporting.
Using neural network architecture, it takes less than 5 minutes to train the system for new product formats.
Inspect 360+ CL provides circumferential 360° inspection of various types of caps, caps and other liquid packaging closures (bottles, vials, etc.). It enables automatic detection of defects in closures, such as, among others: deformations, wrinkles, unscrewing, creases, cracks, discoloration, skewing. It also distinguishes color, and as an option, the system enables analysis of imprints on closures, such as logos, expiration date, BATCH #, QR code.
A great advantage of the system is the ability to image the bottom surface of the cap put on vials, which are used in the production of antibiotics or vaccines (high-margin products) closed in vials.
Optionally, Inspect 360+ CL offers the fill level control. The fill level control module enables the operator setting the required parameters and the permissible margin of error via intuitive touch panel. Based on the given data, the system detects differences in the liquid fill level.
The system meets the requirements of advanced production lines with fast continuous motion (high-volume production).
The Inspect 360+ CL series are a machine vision systems tailored for the cosmetic, pharmaceutical, food industries, and more broadly FMCG.
Learn more about quality control automation per industry:
- quality control vision systems for manufacturers of cosmetics
- quality control vision systems for manufacturers of food and beverage
- quality control vision systems for manufacturers of pills and supplements
Check other KSM Vision's vision systems for your industry:
- machine vision for cosmetic industry by KSM Vision
- machine vision for food industry by KSM Vision
- machine vision for pharma industry by KSM Vision
Advantages:
- 100% control over production, so you can be sure that only error-free products of the highest quality come off your production line
- immediate rejection of defective products from your production line
- traceability of all products - powerful statistical functions give you in-depth insight into the performance of your lines
- centralized qualitative and quantitative product control
- possibility to install on high-speed production lines (capacity up to 40,000 packages per hour)
- user-friendly interface to quickly add products and create a new order (in visual form)
- system training for new products takes less than 5 minutes
- non-contact, non-invasive, fully automatic control
- integration with the IT systems of the production plant in terms of: data exchange, user rights management, reporting
- simultaneous analysis of top, side and bottom surfaces
- compatibility with any production line
- easy integration into new and existing production lines
Options:
- separation system (wedge conveyor)
- separation system (multi-segment rejector)
- liquid/product fill level control
- bottle and vial separation system
- defined trend values and alarms
- detailed reporting
- automatic head reformatting (X, Y axis) to a new order
What do you gain?
- guaranteed consumer safety
- solving labor shortages by introducing automated machine vision based on artificial intelligence in place of manual inspection
- enhancement of brand reputation and trust - consistent delivery of high quality products
- avoiding problems and costs in the downstream process (return of a packing slip, whole batch, container, etc.)
- 100% control over production, so you can be sure that only error-free products of the highest quality come off your production line
- immediate rejection of defective products from your production line
- traceability of all products - powerful statistical functions give you in-depth insight into the performance of your lines
- centralized qualitative and quantitative product control
- possibility to install on high-speed production lines (capacity up to 40,000 packages per hour)
- user-friendly interface to quickly add products and create a new order (in visual form)
- system training for new products takes less than 5 minutes
- non-contact, non-invasive, fully automatic control
- integration with the IT systems of the production plant in terms of: data exchange, user rights management, reporting
- simultaneous analysis of top, side and bottom surfaces
- compatibility with any production line
- easy integration into new and existing production lines
Options:
- separation system (wedge conveyor)
- separation system (multi-segment rejector)
- liquid/product fill level control
- bottle and vial separation system
- defined trend values and alarms
- detailed reporting
- automatic head reformatting (X, Y axis) to a new order
What do you gain?
- guaranteed consumer safety
- solving labor shortages by introducing automated machine vision based on artificial intelligence in place of manual inspection
- enhancement of brand reputation and trust - consistent delivery of high quality products
- avoiding problems and costs in the downstream process (return of a packing slip, whole batch, container, etc.)
Inspect 360+ CL provides full inspection of the quality, safety and content (optional) of caps, corks and other liquid packaging closures, as well as bands (seal) and security films,
The system offers 100% defect inspection in the following areas:
- closure presence
- orientation and position of the closure
- mechanical damage
- curvatures, deformations
- leaks, dirt
- deviations of the lid
- damaged/broken seal
- tightening
- vertical or horizontal cracks
- integrity of the protective tape/foil
- incorrect clamping of the vial
- incorrectly attached safety ring
- (optional) analysis and inspection of colors and imprints on closures (expiration date, SERIES code, QR no., branding)
The system offers 100% defect inspection in the following areas:
- closure presence
- orientation and position of the closure
- mechanical damage
- curvatures, deformations
- leaks, dirt
- deviations of the lid
- damaged/broken seal
- tightening
- vertical or horizontal cracks
- integrity of the protective tape/foil
- incorrect clamping of the vial
- incorrectly attached safety ring
- (optional) analysis and inspection of colors and imprints on closures (expiration date, SERIES code, QR no., branding)
The system is installed on the existing production line above the conveyor.
The system includes the following components:
- measuring head with one digital camera and a set of mirrors, designed LED lighting
- housing with a touch panel (control system allowing the machine to be operated via a touch panel)
- dedicated controller allowing integration with the control logic of the production line
- assembly components for the production line
- pour level sensor (optional)
- reject station (optional)
- bottle and vial separation system (optional)
- automatic head height adjustment system (optional)
Characteristics:
- observation of the top, bottom and side surface of the package with only one camera in 360° (KSM Vision PL patent no. 229618)
- possibilities to classify defective packages
- possibility of installation on high-speed production lines (capacity up to 40,000 packages per hour)
- possibility to connect with production line control signals.
Configurable interface and database
Based on the production specification system interface can be adjusted, including automatic system set-up with data upload by higher-order system (e.g. MES) and additional data upload by line operator. Data collected by the system can be automatically uploaded to higher-order system.
The system includes the following components:
- measuring head with one digital camera and a set of mirrors, designed LED lighting
- housing with a touch panel (control system allowing the machine to be operated via a touch panel)
- dedicated controller allowing integration with the control logic of the production line
- assembly components for the production line
- pour level sensor (optional)
- reject station (optional)
- bottle and vial separation system (optional)
- automatic head height adjustment system (optional)
Characteristics:
- observation of the top, bottom and side surface of the package with only one camera in 360° (KSM Vision PL patent no. 229618)
- possibilities to classify defective packages
- possibility of installation on high-speed production lines (capacity up to 40,000 packages per hour)
- possibility to connect with production line control signals.
Configurable interface and database
Based on the production specification system interface can be adjusted, including automatic system set-up with data upload by higher-order system (e.g. MES) and additional data upload by line operator. Data collected by the system can be automatically uploaded to higher-order system.
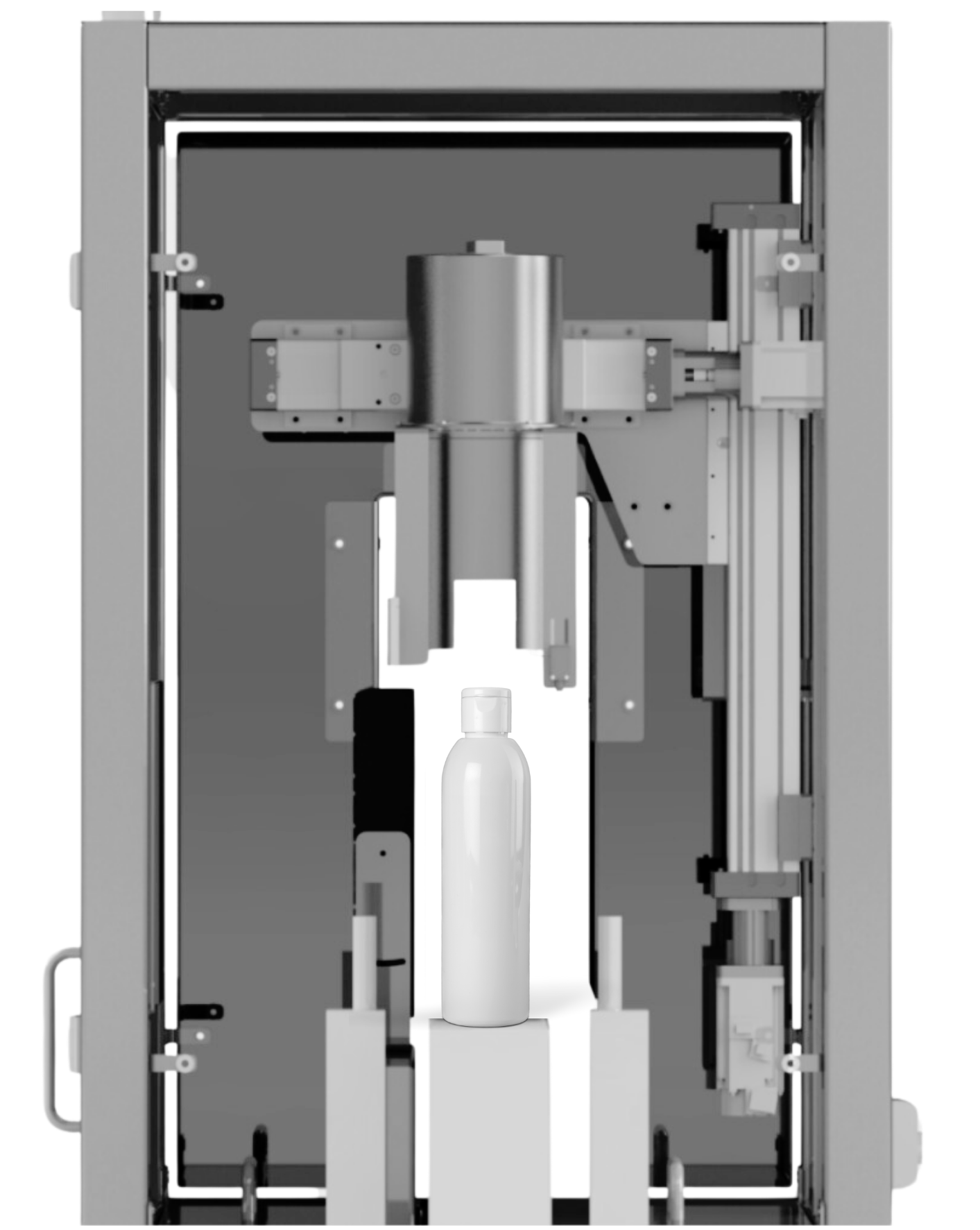
The system's intuitive and functional design allows for easy and quick integration into existing production lines in a non-invasive manner. The innovative design (head with only 1 camera ora set of mirrors allowing simultaneous 360° observation including side and bottom surfaces) is compact, so it can be installed on any production line.
The smart design of the Inspect 360+ CL head is a KSM Vision patent (PL No. 229618).
The Inspect 360+ CL optionally provides a module for inspecting the pouring level of liquids through smart vision inspection. The system can be easily adapted to changes in product height (an extremely useful option when producing bottles of different heights or types). For smooth operation of the module, all that is needed is to set the desired parameters and the acceptable margin of error. With this information, the system is able to detect the fill level and reject underfilled or overfilled bottles.
Inspect 360+ CL:
- meets the requirements of advanced production lines for high-speed continuous packaging production
- is integrated with production plant IT - thanks to the use of neural networks, the system is adapted to corporate requirements for production plant IT systems: data exchange, user rights management, reporting
- can handle a variety of product formats (system training), including vials, bottles and other similar containers (reformatting is fully automated thanks to the automatic head adjustment option)
- has a user-friendly interface for adding new formats and offering visualization of the results in graphical form
The system uses innovative technology that allows simultaneous observation of the top and bottom surfaces of the bottle/vial closure, as well as a 360° view of the side surface of the closure with a single camera.
Controlled objects can move freely between a pair of dedicated mirrors, so the system meets the requirements of high-speed, continuous production lines.
The smart design of the Inspect 360+ CL head is a KSM Vision patent (PL No. 229618).
The Inspect 360+ CL optionally provides a module for inspecting the pouring level of liquids through smart vision inspection. The system can be easily adapted to changes in product height (an extremely useful option when producing bottles of different heights or types). For smooth operation of the module, all that is needed is to set the desired parameters and the acceptable margin of error. With this information, the system is able to detect the fill level and reject underfilled or overfilled bottles.
Inspect 360+ CL:
- meets the requirements of advanced production lines for high-speed continuous packaging production
- is integrated with production plant IT - thanks to the use of neural networks, the system is adapted to corporate requirements for production plant IT systems: data exchange, user rights management, reporting
- can handle a variety of product formats (system training), including vials, bottles and other similar containers (reformatting is fully automated thanks to the automatic head adjustment option)
- has a user-friendly interface for adding new formats and offering visualization of the results in graphical form
The system uses innovative technology that allows simultaneous observation of the top and bottom surfaces of the bottle/vial closure, as well as a 360° view of the side surface of the closure with a single camera.
Controlled objects can move freely between a pair of dedicated mirrors, so the system meets the requirements of high-speed, continuous production lines.
They trust our know-how:
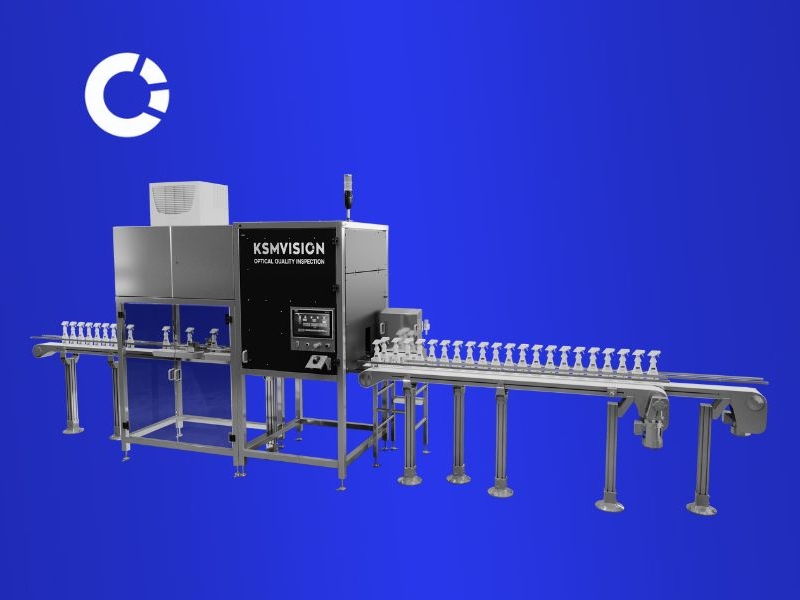