Automatic quality control systems in the food industry
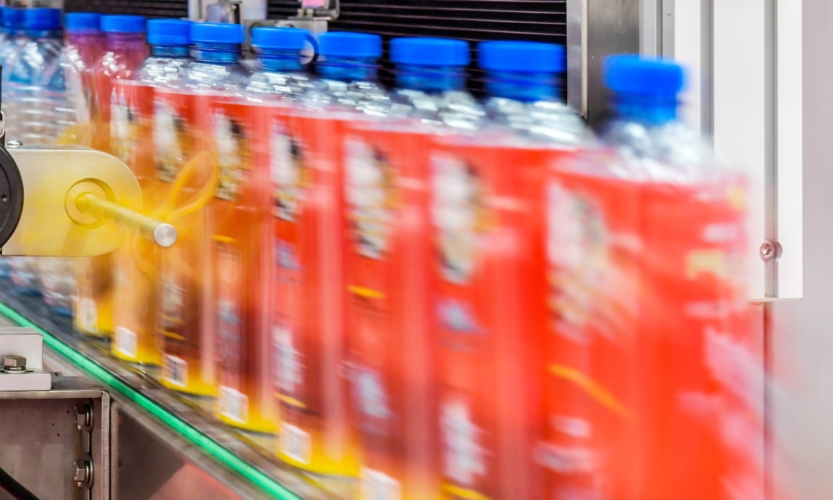
Food quality control is a set of activities that take care of ensuring the highest possible quality of raw materials supplied, overseeing the production process and relying on identifying and eliminating sources of problems. Why is it particularly important in the food industry to invest in automatic quality control?
- Food quality control
- Quality control, why is it so important?
- 10 reasons why quality control is a must in the food industry
- Bet on automation - 10 competitive advantages of automated quality control
- KSM Vision solutions for the food industry - packaging quality control
- X-ray quality control
- KSM Vision - partner in vision-based quality control industry for FMCG
Food quality control
One of the most popular industries where specialized quality control will find its place is the food industry. Food quality control is a set of activities that take care of ensuring the highest possible quality of raw materials supplied, overseeing the production process and consisting of identifying and eliminating sources of problems. Quality control in the food industry is most often the responsibility of employees who perform tests to reveal product defects. However, it is worth remembering that in order for the control to run smoothly, it is necessary to hire many specialists, which is definitely an expensive activity. In addition, the human eye is prone to error, so it is worth betting on modern solutions, which, although initially more expensive, are cost-effective in the long term, and have a smaller margin of error.
Quality control, why is it so important?
Industrial companies have to respond continuously and dynamically to changes in the market, such as an increase in the number of competing companies, increased demand for specific goods and services, and, above all, increasing customer awareness and demands. Taken together, all this means that companies are expected to produce more, operate faster and better. In order to meet business goals and customer expectations, companies need to minimize the number of mistakes they make and, consequently, the amount of costs they incur. One solution is modern quality control systems. Why is precise quality control so important for a food producer and what benefits does it bring?
10 reasons why quality control is a must in the food industry
Quality control is essential in the food industry for several key reasons:
- Consumer safety: Ensuring that food products are safe to eat is the most important goal of quality control.
- Preservation of product quality: Quality control helps maintain consistency and high product quality, which translates into consumer satisfaction.
- Regulatory compliance: The food industry is strictly regulated, and quality control helps ensure compliance with current regulations.
- Protection against contaminants: Quality control helps detect contaminants, such as bacteria or chemicals, that can threaten consumers’ health.
- Minimizing the risk of allergies: With proper quality control, accidental addition of allergens to products can be avoided, which is important for people with food allergies.
- Preventing product defects: Quality control helps detect defects in production, which minimizes the number of defective products reaching the market.
- Maintaining expiration dates: With quality control, product expiration dates can be monitored, helping to avoid the sale of expired products.
- Increasing production efficiency: Quality control allows you to identify areas for improvement in the production process, resulting in lower costs and increased efficiency.
- Minimizing losses: Eliminating defective products and production processes reduces raw material losses and disposal costs.
- Maintaining competitiveness: High product quality and regulatory compliance are key to gaining and maintaining a position in the food market.
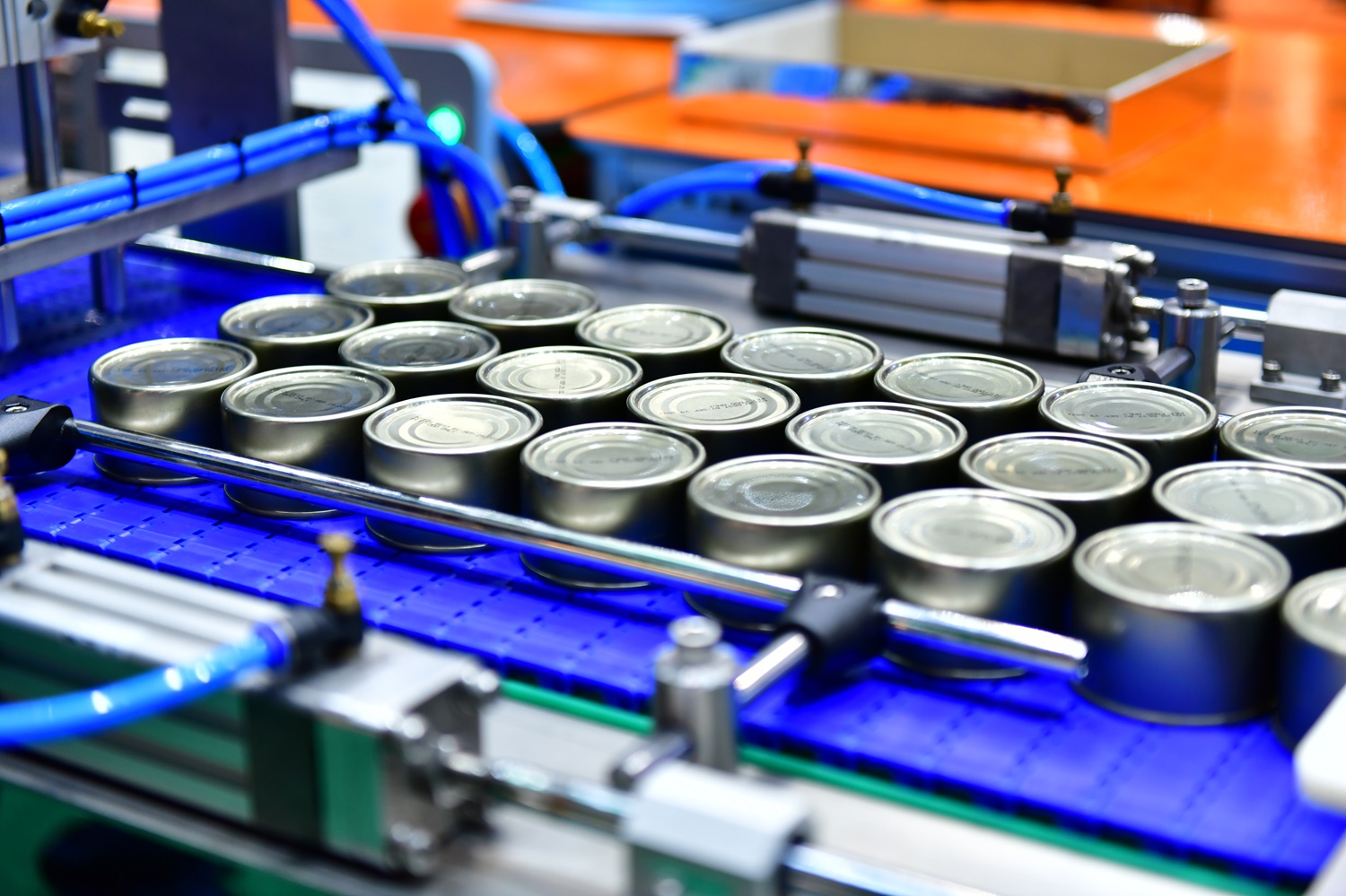
Bet on automation - 10 competitive advantages of automated quality control
Automation is an ever-growing trend that is changing the ways of operations and production in today’s factories. Automation is primarily the use of robots and advanced vision systems so that a company can increase efficiency and precision during the production process. An example is vision-based quality control systems for the food industry.
Here are 10 reasons why vision-based quality control systems are superior to manual inspection in the food industry:
- Higher precision: Vision-based systems are much more precise in detecting even the smallest defects and irregularities in food products.
- Scalability: vision-based systems are capable of processing huge volumes of products per minute, which is impossible to achieve manually. It is also possible to increase the capacity of selected automatic quality control systems relatively quickly by integrating additional system units on additional lines.
- Detection of subtle differences: These systems can recognize subtle differences in shape, color and texture that would escape the human eye.
- Continuous inspection: Vision-based systems provide continuous quality control 24/7, eliminating the need to interrupt production for manual inspections.
- Speed of operation: These systems operate in real time, allowing for immediate response when defects are detected.
- Elimination of human error: Manual inspection is prone to human error, which can be avoided with vision-based systems.
- Cost savings: While the investment in vision systems can be costly initially, they save money in the long run by reducing defective products and rework.
- Regulatory compliance: Vision systems help maintain compliance with stringent regulations and industry standards.
- Improving reputation: By improving product quality and avoiding product defect scandals, a company can gain a better reputation.
- Reduced downtime: By detecting defects immediately, vision-based systems can reduce downtime on the production line, resulting in greater production efficiency and productivity.
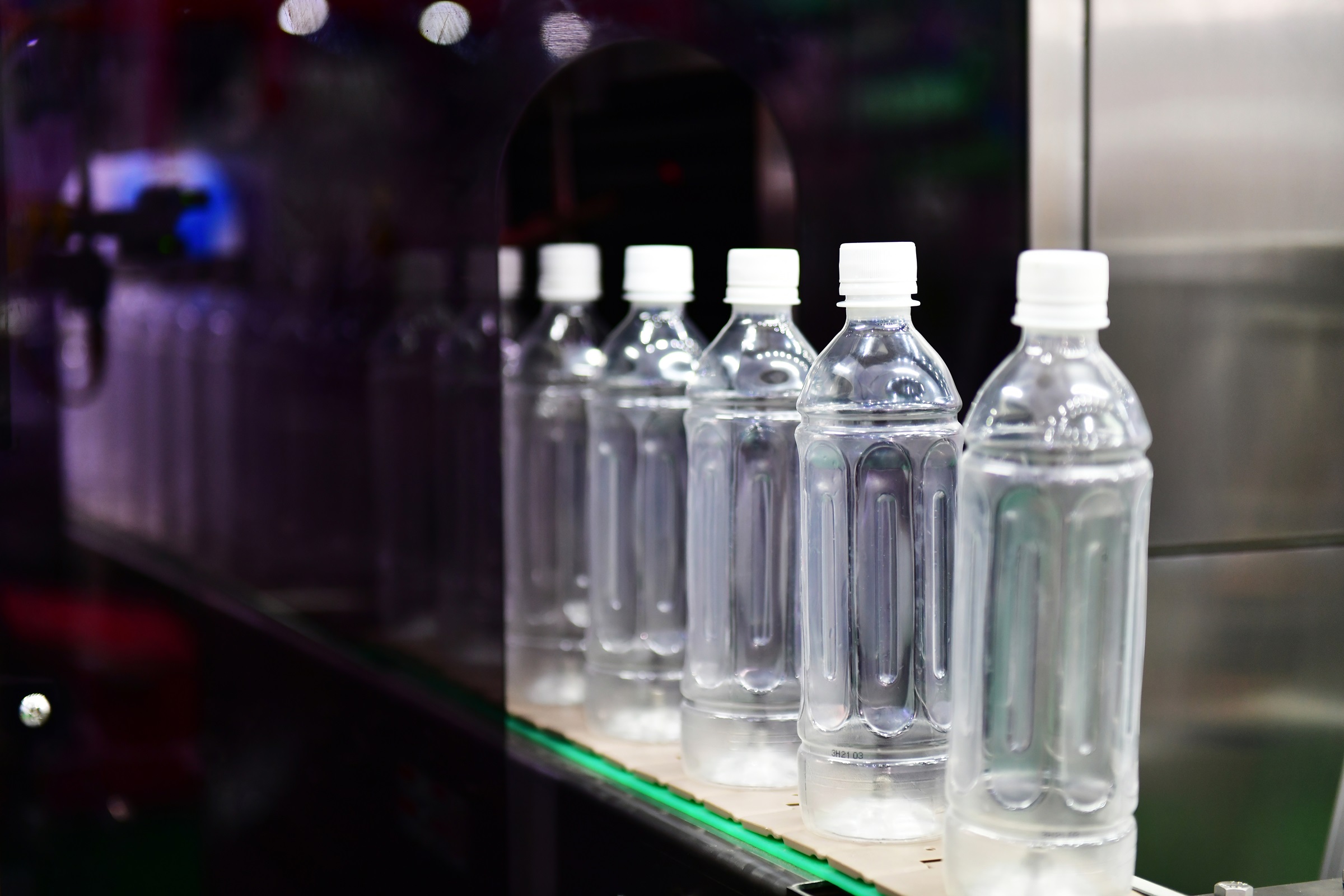
KSM Vision solutions for the food industry - packaging quality control
An example of a solution for automatic quality control systems are the optical inspection systems available from KSM Vision.
At KSM Vision, we design and implement state-of-the-art optical systems for automatic quality control in the food industry that include packaging quality control. The design of the system allows observation of the product in a 360-degree cross section, thanks to the use of modern cameras.
Packaging quality control is the control of the quality of welds in products, control of empty glass packaging (bottles, jars) before dispensing i.e. detection of damage, cracks, scratches or foreign bodies that may be in the product. Quality control of packaging also works well for cans or liquid container closures. The KSM system detects defects such as dirt, dents, missing caps or defective collapsing. Defective or damaged products detected by the system are automatically rejected.
Each of the aforementioned systems can be operated via a data analysis application, which allows clear and remote and remote access to quality control results, reports, trends and alarms.
X-ray quality control
When working with food, packaging is important, but so are the contents themselves. Controlling the quality of the contents of packaging is an incredibly difficult task. However, KSM Vision has undertaken to build such a solution as well, using X-rays.
Quality control using X- Ray by KSM Vision makes it possible to detect unauthorized contaminants or foreign bodies. Foreign bodies can include glass fragments, metal fragments, stones, etc. Examination by radiation is mandatory during the production of food products, since undesirable elements can lead to the exposure of customers to loss of health or life. By using this system, you are assured that a safe product of the highest quality will get into the hands of consumers.
KSM Vision - partner in vision-based quality control industry for FMCG
If you decide to implement an automated system to support production control, look out for those that can be personalized the systems to your plant’s needs. It is important that they are integrated with the equipment and systems already in use. This is the task that the KSM Vision team undertakes.
At KSM Vision, we are a trusted partner in the quality control industry.
We comprehensively integrate and automate our solutions based on machine learning and customized hardware into new and existing production lines, ensuring efficient inspection processes and rapid adaptation.
As a team of more than 25 engineers (software, hardware, data processing) with a start-up approach, we remain flexible in adapting our vision-based quality control systems to customer needs, which is unique among other suppliers.
We combine innovative optics with advanced automation, electronics and dedicated software based on artificial intelligence methods and neural networks. Thanks to the use of machine learning in our solutions, we completely eliminate manual inspection of products, even in stages of the production process where it was previously unavailable. This is our definite competitive advantage as an automated quality control system supplier.
Our solution, trusted by Europe’s EIT Food and EIT Manufacturing and backed by Intel oneAPI for Startups, is built on a foundation of reliability.
We are ISO9001 compliant, so our standards meet global standards of quality and trust.