Eliminating the 8 Wastes of Lean with TIMWOODS
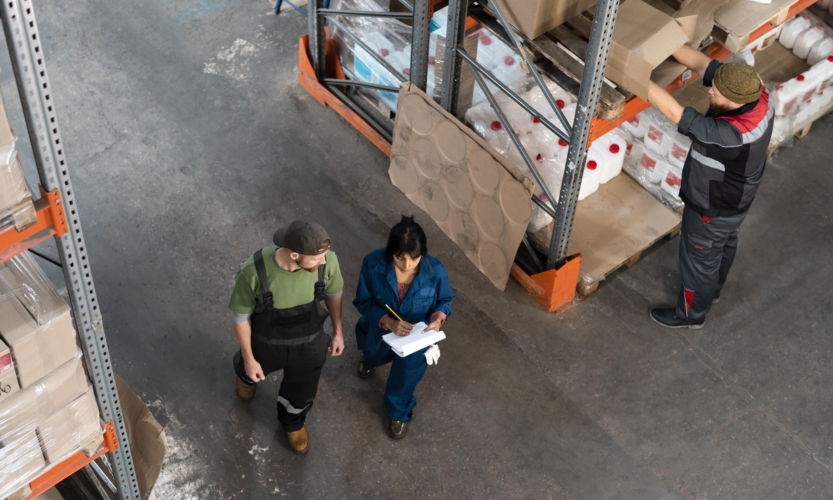
In today’s fast-paced business world, efficiency is the name of the game. Yet, many organizations struggle with hidden inefficiencies that slow processes, increase costs, and frustrate teams. Enter TIMWOODS, a tool rooted in Lean methodology that identifies and addresses the 8 Wastes of Lean, empowering businesses to streamline operations and focus on value creation.
- What is TIMWOODS?
- Breaking Down the 8 Wastes of TIMWOODS
- Why TIMWOODS Matters
- Getting Started with TIMWOODS: Tackling the 8 Wastes of Lean
- Exploring each TIMWOODS waste and actionable solutions to drive efficiency
- How can KSM Vision systems support you in optimizing your processes in accordance with TIMWOODS?
What is TIMWOODS?
TIMWOODS is an acronym representing the 8 common forms of waste found in business processes:
- Transportation
- Inventory
- Motion
- Waiting
- Overproduction
- Overprocessing
- Defects
- Skills (or underutilized talent)
Each of these wastes represents an opportunity for improvement, whether you’re in manufacturing, service delivery, or even creative industries.
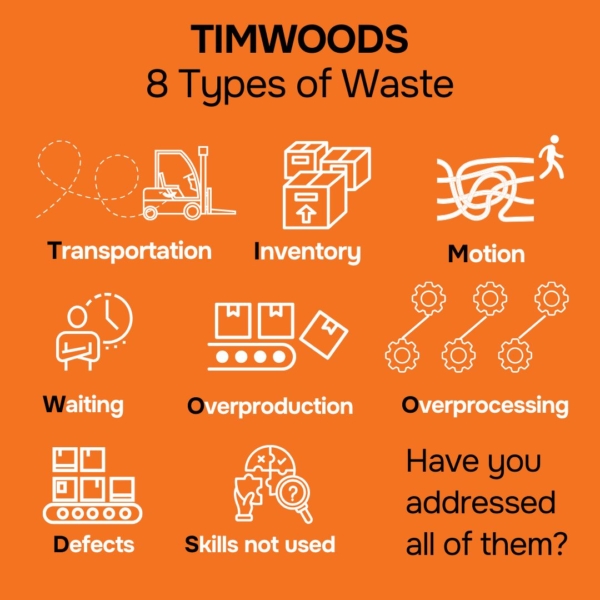
Breaking Down the 8 Wastes of TIMWOODS
- Transportation: Are materials, information, or people being moved unnecessarily? Example: Moving raw materials multiple times before production.
- Inventory: Do you have excess stock sitting idle? Example: Over-ordering supplies that tie up capital.
- Motion: Are employees moving inefficiently to complete tasks? Example: Walking to retrieve tools due to poor workstation layouts.
- Waiting: Are tasks being delayed due to bottlenecks or approvals? Example: A team waiting for data from another department to start work.
- Overproduction: Are you producing more than what’s needed? Example: Manufacturing products ahead of demand, leading to waste.
- Overprocessing: Are you doing more work than necessary? Example: Adding features to a product that customers don’t value.
- Defects: Are mistakes causing rework or wasted effort? Example: Incorrect data entry requiring corrections.
- Skills (Underutilized Talent): Are your team members’ skills and potential going untapped? Example: Highly skilled employees spending time on manual, repetitive tasks.
Why TIMWOODS Matters
Organizations that leverage TIMWOODS to identify and eliminate waste see improved efficiency, reduced costs, and increased employee engagement. By focusing on value-added activities and empowering teams to solve problems, Lean principles help businesses stay competitive and innovative.
By identifying and tackling wastes, businesses can unlock hidden potential, reduce costs, and create value-driven operations. TIMWOODS isn’t just a framework – it’s a roadmap to continuous improvement. As we move forward in a world that demands agility and precision, eliminating the 8 wastes with TIMWOODS can transform your business processes and drive sustainable growth.
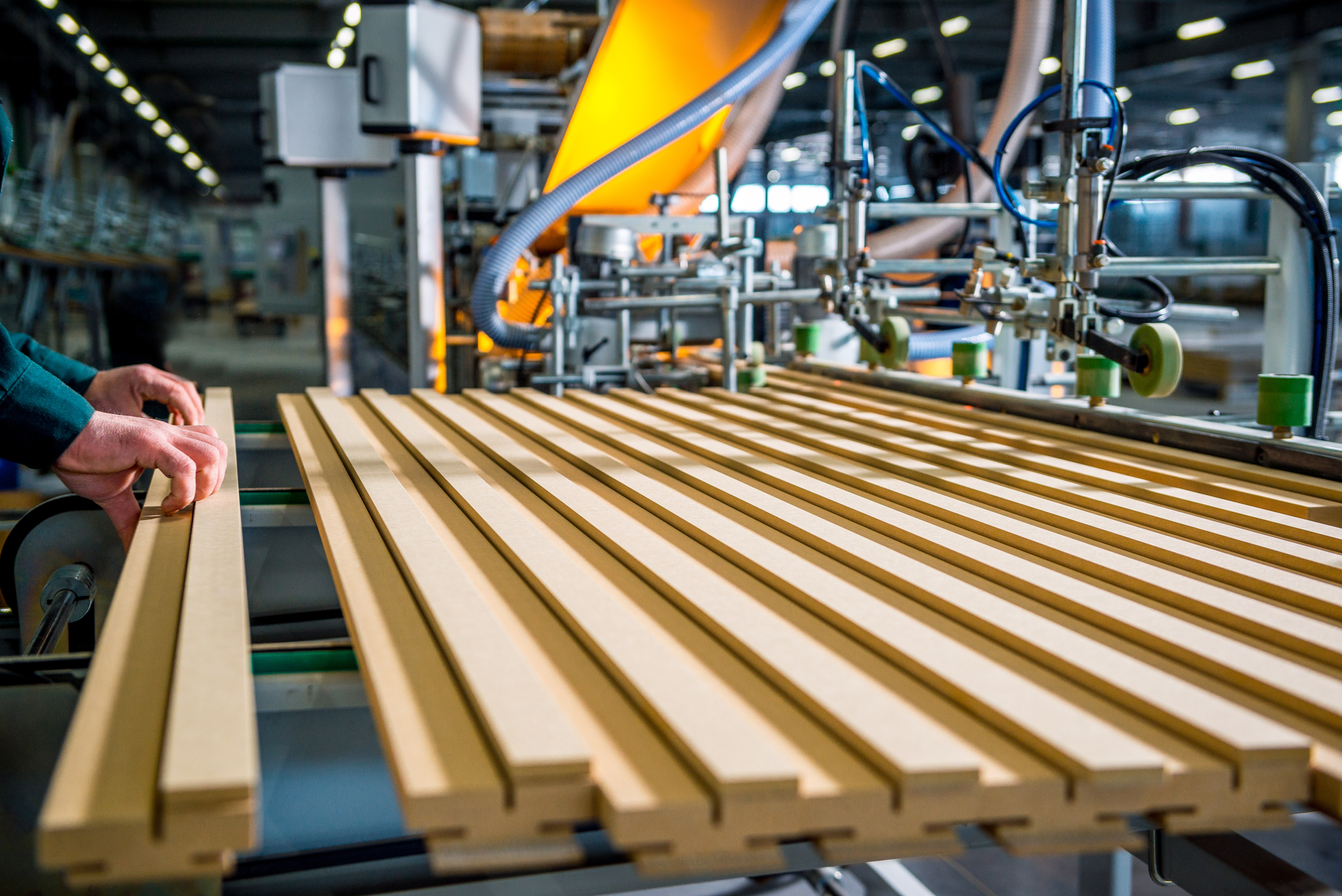
Getting Started with TIMWOODS: Tackling the 8 Wastes of Lean
Which waste resonates most with your business challenges? Eliminating inefficiencies begins with identifying and addressing the 8 wastes of Lean. Here’s how to start working with TIMWOODS to improve your business processes:
- Understand Each Waste: Familiarize yourself with the 8 wastes: Transportation, Inventory, Motion, Waiting, Overproduction, Overprocessing, Defects, and Skills. Know what to look for.
- Map Your Processes: Use tools like process mapping or value stream mapping to visualize workflows and identify areas where waste occurs.
- Engage Your Team: Your employees are closest to the work. Involve them in identifying inefficiencies and brainstorming solutions.
- Audit Your Operations: Conduct regular walkthroughs or Kaizen events to observe processes and spot hidden wastes.
- Prioritize the Wastes: Start with the most significant pain points. Which waste is costing your business the most time or money?
- Set SMART Goals: Define specific, measurable, achievable, relevant, and time-bound objectives for reducing each waste.
- Use Technology: Tools like KSM Vision Systems can help automate defect detection, track inventory, and streamline processes to eliminate waste.
- Commit to Continuous Improvement: Lean isn’t a one-time fix. Regularly review and refine your processes to keep waste at bay.
Start small, stay consistent, and let TIMWOODS guide you toward a more efficient, value-driven operation.
Exploring each TIMWOODS waste and actionable solutions to drive efficiency
Inefficiencies in business processes often hide in plain sight, slowing down operations, wasting resources, and increasing costs. The Lean methodology’s TIMWOODS framework helps identify and address these inefficiencies. Let’s break down the problems each waste presents and explore actionable solutions to drive efficiency.
1️⃣ Transportation: Wasted movement of materials. ➡ Optimize layouts to reduce unnecessary transport.
2️⃣ Inventory: Excess stock taking up space. ➡ Use tools to track and forecast demand accurately.
3️⃣ Motion: Unnecessary movement of people. ➡ Streamline workflows and organize workstations.
4️⃣ Waiting: Idle time from bottlenecks. ➡ Communicate clear workflows to keep things moving.
5️⃣ Overproduction: Making more than needed. ➡ Align production with real customer demand.
6️⃣ Overprocessing: Overcomplicating processes. ➡ Simplify and invest in quality tools.
7️⃣ Defects: Errors causing rework. ➡ Fix root causes and improve quality control.
8️⃣ Skills: Ignoring employee talent. ➡ Encourage creativity and invest in professional growth.
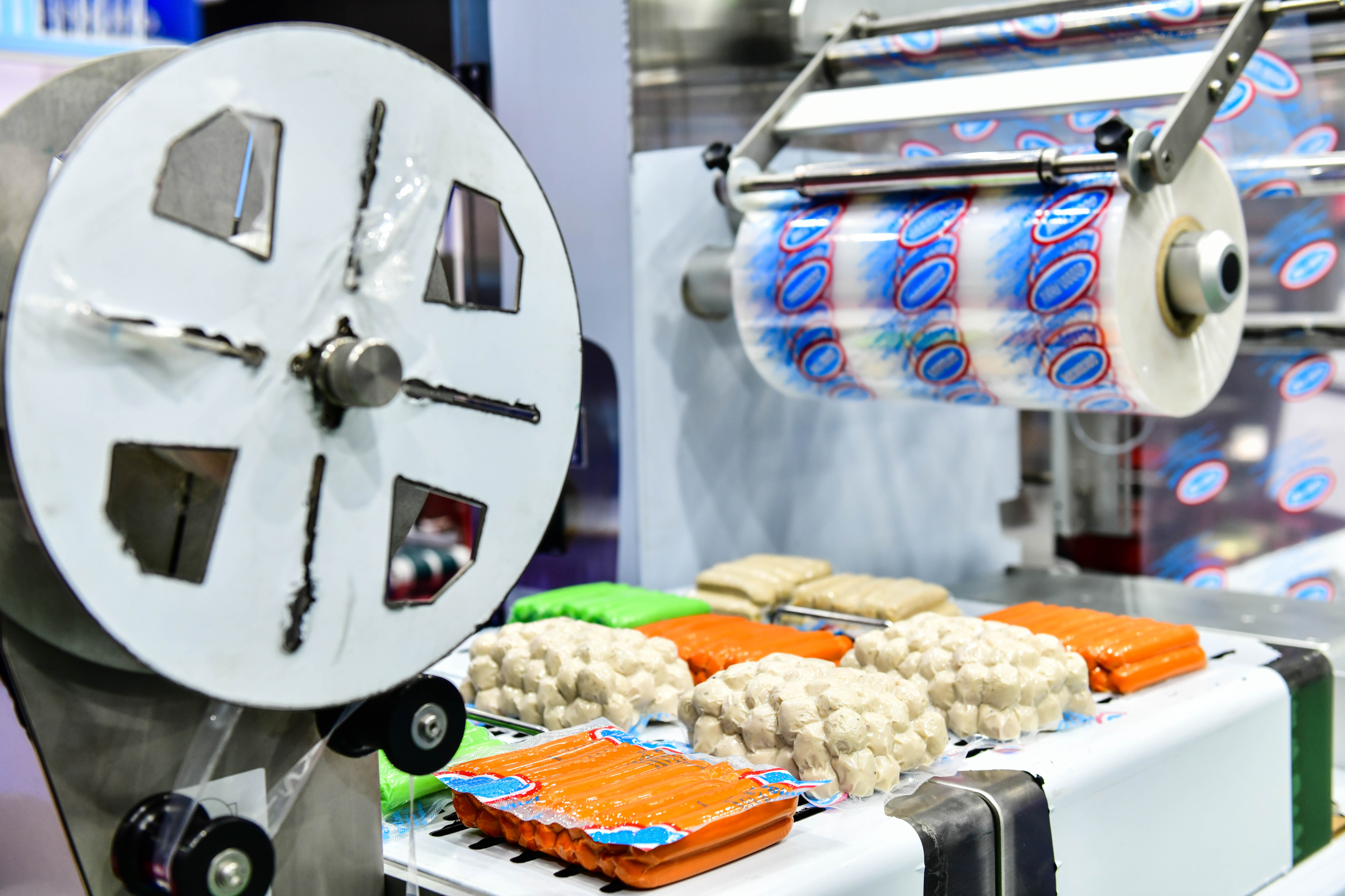
How can KSM Vision systems support you in optimizing your processes in accordance with TIMWOODS?
KSM Vision develops proprietary machine learning-based vision quality control systems and comprehensively integrates them into new and existing production lines. Production automation using vision systems based on deep neural networks (deep learning AI) – such KSM Vision systems – enables elimination of the manual inspection from the factory’s quality control processes, increasing manufacturer processes’ profitability and scalability.
The flexibility of KSM Vision systems empowered with neural networks makes it possible to train AI models and adapt the vision system to changing production requirements (e.g. new product formats, new types of defects, other processes), offering quality control solutions going far above standard smart cameras. KSM Vision systems collect and analyze real data from production lines, basing statistics on large collections and AI data mining algorithms.
- Motion: KSMVision automates repetitive tasks, reducing manual effort.
- Waiting: KSM Vision pinpoints and even prevents production delays with real-time alerts about shortages, defects or mistakes.
- Overprocessing: KSM Vision systems standardize and simplify quality checks.
- Defects: (quite obviously) KSM Vision detects defects early, saving time and costs, and minimizing production risks.
- Skills: KSM Vision frees employees to focus on higher-value work in the factory.