Smart cameras or AI-driven vision solutions for quality control? Is there any difference? Find out.
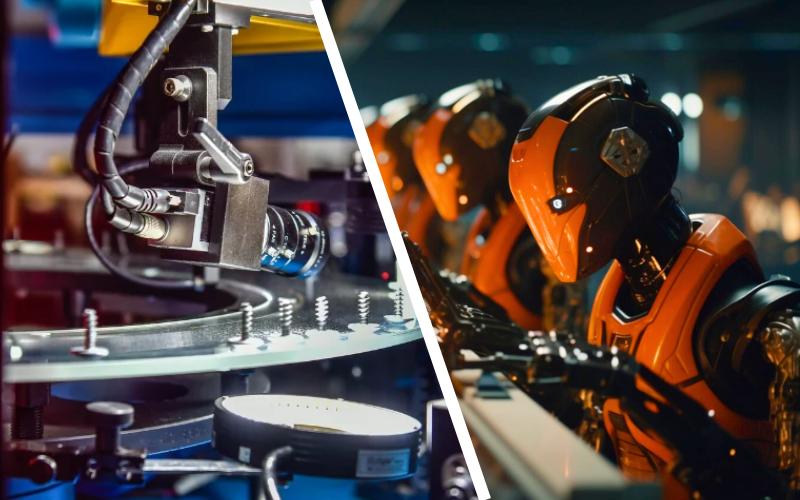
In modern industrial settings, ensuring product quality is paramount to maintaining customer satisfaction and operational efficiency. Smart cameras and AI-driven vision systems have emerged as indispensable tools for quality control, offering advanced capabilities for inspecting, detecting, and analyzing defects in manufactured goods. These automated vision inspection systems are often considered the same thing, no matter the approach to feature extraction. However, there are some key distinctions between smart cameras and vision systems using deep learning AI. Learn the difference.
Smart cameras for quality control
Smart cameras designed for quality control play a crucial role in modern industrial environments by efficiently inspecting products or components. These cameras work by capturing images of items passing through the production line, utilizing embedded processing to analyze the visual data in real-time. Through predefined algorithms, smart cameras can detect various defects, irregularities, or deviations from desired specifications. There are different types of smart cameras tailored to specific inspection needs, including 2D and 3D variants. While 2D smart cameras focus on surface inspection, 3D models provide additional depth information for accurate dimensional analysis. By analyzing surface quality, smart cameras ensure that products meet rigorous quality standards before reaching consumers.
Integrated with programmable logic controllers (PLCs) or industrial networks, smart cameras seamlessly integrate into automated manufacturing systems. This integration facilitates swift communication and enables immediate corrective actions in response to detected defects. The real-time nature of smart camera inspection enhances manufacturing efficiency by minimizing production downtime and reducing the likelihood of defective products reaching the market.
Some of the most popular brands offering smart camera systems for quality control include: Cognex Corporation, Keyence Corporation, Teledyne DALSA, Omron Corporation, and Sick AG.
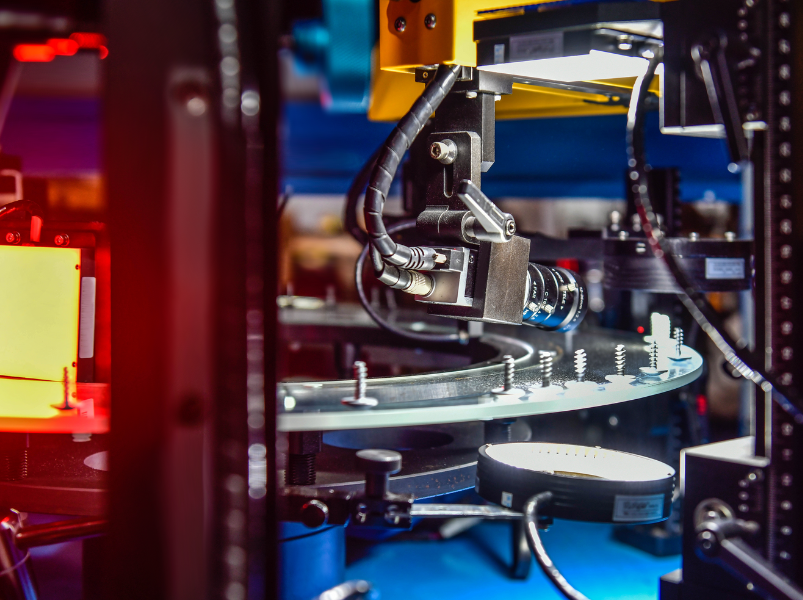
Smart cameras have it all? Not really.
The smart cameras for quality control do not ‘have it all’. Although the smart cameras have indeed emerged as indispensable tools for quality control, offering advanced capabilities for inspecting, detecting, and analyzing defects in manufactured goods – they are smart! – there is one major difference between them and more advanced AI-driven vision systems, and that one difference brings on several consequences.
The main difference between smart cameras and AI-driven (deep learning AI) vision systems for quality control lies in their approach to image analysis and decision-making. Smart cameras primarily rely on predefined algorithms and rule-based logic to process images and identify defects, providing a deterministic approach to inspection. In contrast, AI-driven vision systems leverage artificial intelligence (AI) techniques, particularly machine learning algorithms, to analyze visual data and make decisions based on learned patterns and features.
AI-driven vision systems have the capability to learn from labeled datasets, allowing them to adapt and improve over time through continuous training and exposure to new data. This adaptive learning capability enables AI-driven systems to handle complex inspection tasks with greater flexibility and accuracy compared to rule-based smart cameras. Additionally, AI-driven vision systems offer the potential for more sophisticated defect detection and classification, as they can recognize subtle variations and anomalies in visual data that may not be easily captured by predefined algorithms alone.
KSM Vision is one of the few producers of automated vision systems who offers the quality control systems based on the neural architecture (deep learning AI) in their product portfolio.
Deep learning AI in quality inspection
Deep learning, a subset of machine learning, focuses on using neural networks with many layers to learn from data. Unlike traditional machine learning algorithms, deep learning models automatically extract features from raw data, reducing the need for manual feature engineering.
Deep learning architectures, such as convolutional neural networks (CNNs) and recurrent neural networks (RNNs), excel in tasks like image recognition, natural language processing, and sequential data analysis. While deep learning is powerful for tasks requiring high-level abstraction and complex patterns, traditional machine learning techniques rely more on feature engineering and are often used for structured data with clear features.
Deep learning models typically require large amounts of labeled data and computational resources for training, making them more computationally intensive compared to many machine learning algorithms. Their ability to learn intricate patterns and representations has made them increasingly popular in recent years. In the area of the quality inspection this ability unlocks advanced analytics, adaptive learning, and predictive prowess, boosting efficiency and satisfying changing consumer expectations for sustainability and product excellence.
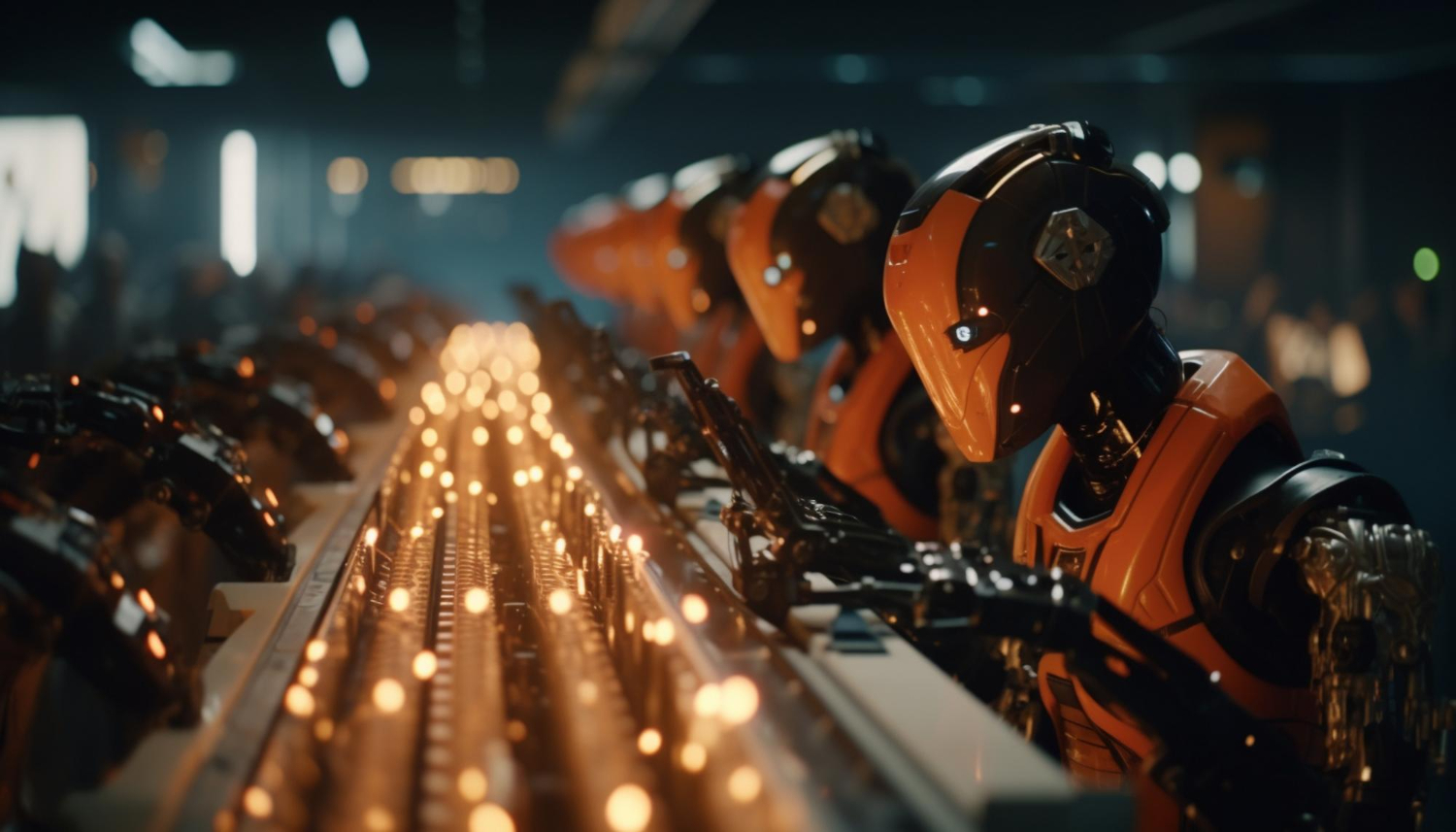
Smart cameras or AI-driven vision systems for quality control - what to choose?
The answer to such question is usually ‘it depends on your needs’. However, in this case the answer should be rather – ‘it depends on the assumed investment horizon, the anticipated growth, and your level of risk propensity.’
Smart cameras provide simplicity and real-time operation for basic inspection tasks. On top of that, through the utilization of artificial intelligence and machine learning techniques, AI-driven vision systems offer:
- enhanced adaptability,
- greater flexibility,
- the potential for advanced customizations and applications,
- high scalability.
Why is that important in the context of anticipated investment horizon, business growth, or risk propensity? Because in the era of the shift towards enhancing production efficiency while addressing ecological concerns and staying up to date with consumer trends, a modern high-volume manufacturer cannot, or should not, ignore none of the above-mentioned factors. The Quality Control Manager or Production Manager with limited risk propensity, may want to consider constantly changing manufacturing environment and market trends when choosing an automated vision solution for their plant. One may find greater sense of… security – plus real benefit – in the deep learning AI-based automated vision solution for quality control, which will be long-term and scalable.
It is not always essential to incorporate deep learning AI in the quality inspection systems, e.g. some OCR-based systems do not always require such technologically advanced solutions. However, in the applications where potential defects may vary heavily (e.g. defects on natural wood in furniture industry, pills in pharma production), or the quality inspection requirements change overtime, deep learning AI offers long-term benefit.
When choosing the automated vision solution, it is also worth analyzing the plant’s needs in the area of IT systems. If you’re looking for a customizable solution that will enable integration with the plant’s IT in terms of data exchange, reporting, or user permissions, the deep machine learning will offer greater flexibility.
Trends in manufacturing versus automated vision system choice
The current manufacturing trends include i.a.:
- Reducing production waste (recalls, material waste, etc.) thanks to comprehensive inspection of products (both smart cameras and AI-driven vision systems can do it),
- Automation, robotization and digitization at every stage of the production process to minimize or even eliminate manual work (smart cameras can meet this need to some extent, vision systems using deep learning AI have much greater potential),
- Corporate manufacturers putting strong focus on the software scalability and efficiency (only machine-learning vision systems can offer that),
- Data intelligence and in-depth traceability features in these systems (only machine-learning vision systems can offer that),
- Growing demand on tailored solutions which offer greater flexibility and adaptability in terms of constantly changing production requirements – changed labels, new packaging formats, ‘zero waste’ policies, etc. (only machine-learning vision systems can offer that).
Opting for AI-driven vision systems can enable manufacturers to leverage advanced analytics, adaptive learning, and predictive capabilities to not only enhance production efficiency but also meet evolving consumer demands for sustainability and product quality.
Pros and cons of both solutions
The software architecture and capabilities differ between smart camera-based vision systems and machine-learning-based vision systems. Here’s a breakdown of the key differences:
- Smart Camera-Based Automated Vision Systems:
- Predefined Algorithms: Smart camera systems typically utilize predefined algorithms and rule-based logic to perform basic image processing and analysis tasks. These algorithms are designed to execute specific inspection routines, such as edge detection, blob analysis, and template matching, without the need for extensive programming or customization.
- Embedded Software: Smart cameras are equipped with embedded software that controls image acquisition, processing, and communication functions within the camera itself. The software is optimized for real-time operation and often includes a graphical user interface (GUI) for configuring inspection parameters and viewing results.
- Limited Flexibility: While smart camera software offers simplicity and ease of use, it may have limited flexibility for handling complex inspection scenarios or adapting to changing requirements. Users are typically restricted to the predefined algorithms and features provided by the camera manufacturer.
- Deep learning AI-driven Automated Vision Systems:
- Training and Learning Capabilities: Machine learning-based vision systems leverage advanced software algorithms, particularly deep learning techniques, to analyze and learn from large datasets of labeled images. These systems can be trained to recognize patterns, features, and anomalies in visual data, enabling more sophisticated and adaptive inspection capabilities.
- Customizable Models: Unlike smart camera systems, machine learning-based vision systems offer greater flexibility and customization options. Users can train and fine-tune machine learning models to suit specific inspection tasks, adjusting parameters, architectures, and training data to improve accuracy and performance.
- Integration with Development Frameworks: Machine learning-based vision systems often integrate with popular development frameworks and libraries for deep learning, such as TensorFlow, PyTorch, or OpenCV. This allows users to leverage a wide range of tools, algorithms, and resources for building, training, and deploying machine learning models tailored to their quality control requirements.
- Continuous Improvement: Machine learning-based vision systems have the ability to continuously learn and improve over time as they are exposed to more data and feedback. This adaptive learning capability enables the system to adapt to changes in product designs, manufacturing processes, or inspection criteria, leading to enhanced accuracy and performance.
No matter the choice, if delivered by a credible and proven supplier, each of these solutions is robust and reliable, offering top defect detection accuracy. In terms of pricing the solutions are comparable, and the factor that determines the price level to the greatest extent is the brand recognition.
More about: smart quality control systems in smart factories
To sum up
In modern industrial settings, ensuring product quality is paramount to maintaining customer satisfaction and operational efficiency. Smart cameras and machine-learning-based vision systems have emerged as indispensable tools for quality control, offering advanced capabilities for inspecting, detecting, and analyzing defects in manufactured goods.
While both technologies serve the common goal of quality assurance, they employ distinct approaches and functionalities. Smart cameras rely on predefined algorithms and rule-based logic for image processing and analysis, providing simplicity and real-time operation. In contrast, machine-learning-based vision systems – watch out, using deep learning AI, not any ‘machine learning’ algorithms! – leverage advanced algorithms, particularly deep learning techniques, to analyze and interpret visual data, offering adaptive learning capabilities and customization for handling diverse quality control tasks.